Discover Premium Ceramic Products | Durability & Elegance United | Advanced Ceramics
PRODUCT PARAMETERS
Description
Overview of Boron Nitride Ceramic
Boron Nitride (BN) ceramic is a unique material renowned for its exceptional properties, making it highly valuable in various industrial applications. It exists in multiple forms, primarily hexagonal boron nitride (h-BN), cubic boron nitride (c-BN), and wurtzite boron nitride (w-BN). Hexagonal BN, the most common form, is often compared to graphite due to its lubricious and thermally conductive yet electrically insulating nature. Boron Nitride ceramics are synthesized under high temperatures and pressures, offering a rare combination of properties not found in many other materials.
Features of Boron Nitride Ceramic
Thermal Conductivity: Excellent thermal conductivity, especially in the hexagonal form, allowing efficient heat dissipation.
Electrical Insulation: Outstanding electrical insulation properties make it ideal for electrical applications requiring thermal management.
Chemical Stability: Highly resistant to chemical attacks, including strong acids and bases, ensuring durability in harsh environments.
Thermal Shock Resistance: Superior resistance to thermal shock, enabling it to withstand rapid temperature changes without cracking.
Mechanical Strength: Good mechanical strength at both room and elevated temperatures, although this can vary with the form of BN.
Lubricity: Self-lubricating property due to its layered structure, which reduces friction and wear in moving parts.
Non-Toxic: Safe to use in various settings, including medical and food processing industries, due to its non-toxic nature.
High-Temperature Performance: Maintains stability at extremely high temperatures, exceeding 1000°C in inert atmospheres, making it suitable for refractory applications.
(PBN Heat Conduction Pyrolytic Boron Nitride Graphite Coat Evaporation Boat Ceramic Crucibe)
Specification of PBN Heat Conduction Pyrolytic Boron Nitride Graphite Coat Evaporation Boat Ceramic Crucibe
The PBN Heat Conduction Pyrolytic Boron Nitride Graphite Coat Evaporation Boat Ceramic Crucible is engineered for high-temperature applications. It combines Pyrolytic Boron Nitride (PBN) with a graphite coating. This design ensures efficient heat transfer and durability. The crucible operates under extreme conditions, handling temperatures up to 1800°C in inert environments. Its thermal conductivity reaches 60 W/m·K, enabling rapid, uniform heating. Standard dimensions include lengths from 50mm to 200mm. Wall thickness ranges between 2mm and 5mm. The graphite coat enhances thermal distribution and reduces material sticking during evaporation processes.
The crucible resists thermal shock. It maintains structural integrity during rapid temperature changes. This prevents cracking or warping. The PBN base material offers high chemical inertness. It does not react with most metals, semiconductors, or molten materials. This minimizes contamination in sensitive processes. The graphite layer adds wear resistance. It extends the crucible’s lifespan even under repeated use.
This product suits semiconductor manufacturing. It is ideal for thin-film deposition, vacuum evaporation, and molecular beam epitaxy. Laboratories use it for material research requiring precise thermal management. Industries like optics and electronics rely on it for coating production. The crucible works in both continuous and intermittent high-heat operations.
Its design prioritizes user convenience. The smooth surface allows easy cleaning. The lightweight structure reduces handling strain. Custom sizes are available for specialized setups. The material’s low outgassing properties ensure vacuum stability. This is critical for processes demanding minimal environmental interference.
Performance consistency is a key advantage. The crucible delivers repeatable results over multiple cycles. It reduces downtime caused by frequent replacements. Operational costs stay low due to its longevity. Users benefit from reliable heat management and minimal maintenance.
The combination of PBN and graphite addresses common industry challenges. It eliminates issues like uneven heating or material adhesion. This improves process efficiency and output quality. The crucible meets stringent industrial standards for purity and thermal performance. It is compatible with standard evaporation systems. No modifications are needed for integration.
This product is a practical solution for high-precision, high-temperature applications. It bridges the gap between advanced material science and industrial practicality. Users achieve optimal results without compromising equipment reliability.
(PBN Heat Conduction Pyrolytic Boron Nitride Graphite Coat Evaporation Boat Ceramic Crucibe)
Applications of PBN Heat Conduction Pyrolytic Boron Nitride Graphite Coat Evaporation Boat Ceramic Crucibe
The PBN Heat Transmission Pyrolytic Boron Nitride Graphite Layer Dissipation Watercraft Ceramic Crucible is a high-performance product created for demanding industrial applications. It combines pyrolytic boron nitride (PBN) with graphite finishings to create a resilient, heat-resistant solution. This item masters atmospheres calling for severe thermal stability and chemical inertness. It is commonly made use of in processes like vacuum evaporation, thin-film deposition, and semiconductor production.
The crucible’s framework ensures efficient warmth circulation. The PBN layer provides superb thermal conductivity while resisting responses with liquified steels or harsh materials. The graphite covering adds toughness and decreases wear during duplicated use. This makes the crucible ideal for managing products like light weight aluminum, gallium, and other metals at high temperatures.
In semiconductor production, the crucible is crucial for vaporizing products to produce slim movies on silicon wafers. Its reduced thermal expansion avoids cracking under fast temperature modifications. This reliability makes sure regular cause processes such as molecular beam epitaxy (MBE). The product’s pureness avoids contamination, which is vital for creating high-quality electronic parts.
The dissipation boat design permits accurate control over material deposition. This is important for applications in optics, where uniform coatings on lenses or mirrors are needed. The crucible’s resistance to thermal shock makes it suitable for sectors such as aerospace, where components deal with extreme problems.
Another vital usage is in LED manufacturing. The crucible’s capacity to handle high temperatures without degrading guarantees lasting performance during gallium nitride deposition. It also sustains study labs servicing advanced products, supplying a recyclable option that lowers operational costs.
The graphite finishing extends the crucible’s life expectancy by lessening erosion from reactive products. This lowers downtime for substitutes, enhancing effectiveness in commercial settings. Its compatibility with vacuum cleaner systems makes it a functional device for both large-scale production and specialized experiments.
The PBN Warm Transmission Crucible satisfies the needs of sectors prioritizing precision and longevity. Its layout addresses difficulties in high-temperature processing, providing a dependable option for modern-day innovation advancement.
Company Introduction
Advanced Ceramics founded on October 17, 2014, is a high-tech enterprise committed to the research and development, production, processing, sales and technical services of ceramic relative materials and products.. Since its establishment in 2014, the company has been committed to providing customers with the best products and services, and has become a leader in the industry through continuous technological innovation and strict quality management.
Our products includes but not limited to Silicon carbide ceramic products, Boron Carbide Ceramic Products, Boron Nitride Ceramic Products, Silicon Carbide Ceramic Products, Silicon Nitride Ceramic Products, Zirconium Dioxide Ceramic Products, Quartz Products, etc. Please feel free to contact us.(nanotrun@yahoo.com)
Payment Methods
T/T, Western Union, Paypal, Credit Card etc.
Shipment Methods
By air, by sea, by express, as customers request.
5 FAQs of PBN Heat Conduction Pyrolytic Boron Nitride Graphite Coat Evaporation Boat Ceramic Crucibe
What is a PBN heat conduction crucible used for?
This crucible is used for vaporizing materials in high-temperature settings. It works in processes like thin-film deposition. It handles metals, semiconductors, and ceramics. Industries like electronics and optics rely on it for coating components.
Why pick a PBN-coated graphite crucible over others?
The coating boosts heat transfer. It spreads heat evenly across the surface. This prevents hot spots. The material lasts longer under extreme heat. It resists chemical reactions. This keeps the melted materials pure.
How hot can this crucible get before failing?
It handles temperatures between 1800°C and 2200°C. The exact limit depends on the model. It stays stable in continuous high-heat operations. It won’t crack or warp easily.
What steps keep the crucible in good shape?
Avoid dropping or hitting it. Clean it after each use. Remove leftover residues gently. Don’t expose it to sudden temperature changes. Store it dry. Keep it away from moisture or harsh chemicals.
Is this crucible better than regular graphite or ceramic ones?
Yes. The PBN layer improves heat distribution. Regular graphite degrades faster. Ceramic crucibles crack under rapid heating. This version resists thermal shock. It also reduces contamination risks. This makes results more reliable.
(PBN Heat Conduction Pyrolytic Boron Nitride Graphite Coat Evaporation Boat Ceramic Crucibe)
REQUEST A QUOTE
RELATED PRODUCTS
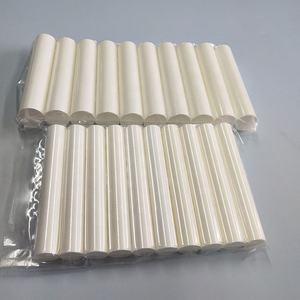
Custom White High Temperature Resistant Insulation Boron Nitride BN Ceramic Tube
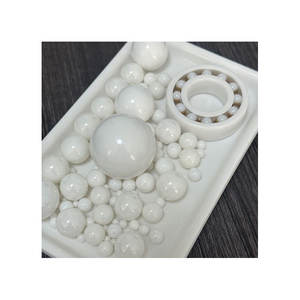
High Purity Boron Nitride Ceramic Crucible Hot Pressed for Semiconductor Industry Includes Cutting Service
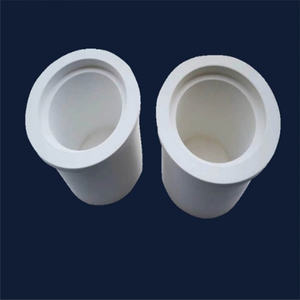
High Purity Boron Nitride Ceramic Shaft Rod BN Ceramic Cylinder
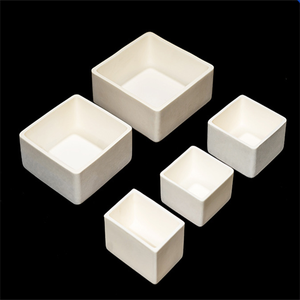
High Temperature Pyrolytic Boron Nitride PBN Ceramic Heater for Vacuum Chamber
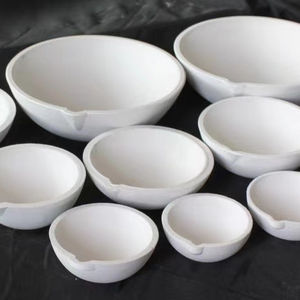
High Quality One End Open and the Other End Closed Boron Nitride Ceramic Tube BN Thermocouple protection Pipe
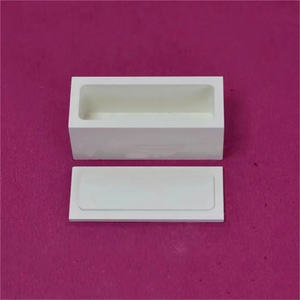