Discover Premium Ceramic Products | Durability & Elegance United | Advanced Ceramics
PRODUCT PARAMETERS
Description
Introduction to Quartz Ceramic Products
Quartz ceramic, also known as fused quartz ceramic or pure silicon ceramic, is an advanced ceramic material made of pure silicon dioxide (SiO₂). It is made by melting high-purity quartz sand at high temperature and then cooling and solidifying it. It has unique physical and chemical properties, making it an ideal choice for many high-tech applications. Quartz ceramic products are widely used in semiconductor manufacturing, optics, electronics, chemical industry and high-temperature industries.
Characteristics and advantages of quartz ceramics
Extremely high thermal stability: Quartz ceramics can remain stable under extreme temperature conditions. They are not only resistant to high temperatures, but also show excellent thermal shock resistance in rapid temperature changes.
Low thermal expansion coefficient: Due to its low thermal expansion coefficient, quartz ceramics have good dimensional stability when the temperature changes and are not easy to deform or crack.
Excellent electrical insulation: Provides excellent electrical insulation performance and is suitable for applications requiring high voltage isolation.
High transparency: It has good light transmittance in a wide band from ultraviolet to infrared, and is particularly suitable for applications such as optical windows and lenses.
Chemical stability: Excellent resistance to most acids, alkalis and other corrosive substances, and almost unaffected by other chemicals except hydrofluoric acid and phosphoric acid.
Mechanical strength: Although quartz ceramic is not as hard as some other types of ceramics, it still has enough mechanical strength to meet the needs of many application scenarios.
High UV transmittance: It has high transmittance in the ultraviolet region, which makes it very useful in UV curing equipment and UV spectrometers.
(Fused Silica Quartz Ceramic Roller for Tile Kiln Furnace Ceramic Roller)
Specifications of Fused Silica Quartz Ceramic Roller for Tile Kiln Furnace Ceramic Roller
The Molten Silica Quartz Ceramic Roller is constructed for ceramic tile kiln heaters. It operates in high-temperature settings. The roller withstands temperature levels as much as 1250 ° C. It resists thermal shock efficiently. Rapid temperature changes cause no fractures. The material is pure merged silica quartz. This makes sure chemical stability. It does not respond with kiln gases or glazes. Contamination dangers stay low. The roller has high mechanical stamina. It lugs hefty floor tile lots without flexing. Low thermal development keeps its shape stable. Performance remains consistent in time. The surface is smooth. Ceramic tiles move equally without surface damage. Diameters vary from 30 mm to 120 mm. Sizes reach up to 3000 mm. Custom dimensions fit certain demands. The roller satisfies ceramic market requirements. It lasts longer than metal or conventional ceramic rollers. Upkeep demands are very little. Downtime lowers. Costs stay reduced. The product operates in electrical, gas, or passage kilns. Installment is simple. It fits existing kiln arrangements. The roller improves floor tile manufacturing performance. Floor tile quality remains high. Problems reduce. Outcome increases. Material purity goes beyond 99.9%. This stops bubbles or impurities. Density keeps above 2.2 g/cm THREE. Wear resistance is solid. Misuse causes no damages. Running life expands past 5 years. Warm cycles do not compromise structure. Energy intake stays reduced. Warmth transfer is effective. Manufacturing rates rise. The roller matches fast-firing kilns. It manages constant start-stop cycles. No preheating is required. Operators save time. Technical assistance is available. Custom-made options match unique kiln styles. Checking ensures dependability. Examples validate performance. Bulk orders have discounts. Shipment timelines are adaptable. The product is a sensible upgrade for floor tile suppliers.
(Fused Silica Quartz Ceramic Roller for Tile Kiln Furnace Ceramic Roller)
Applications of Fused Silica Quartz Ceramic Roller for Tile Kiln Furnace Ceramic Roller
Integrated silica quartz ceramic rollers play an essential function in tile kiln furnaces. These rollers support and deliver ceramic tiles with high-temperature firing processes. They manage extreme heat up to 1300 ° C without bending. This makes them perfect for maintaining steady manufacturing problems. Their low thermal expansion prevents cracks under rapid temperature level modifications. This makes certain regular tile top quality throughout shooting.
The material’s high pureness lowers contamination risks. It stands up to chain reactions with lusters or gases in the kiln. This keeps ceramic tile surface areas clean and defect-free. The rollers’ smooth surface lessens friction. Ceramic tiles relocate equally without scrapes or irregular healing. This boosts the final product’s appearance and architectural stability.
Merged silica quartz ceramic rollers last longer than conventional products. They endure mechanical anxiety from heavy ceramic tile loads. Their wear resistance cuts downtime for replacements. This enhances kiln effectiveness and decreases maintenance costs. The rollers also save energy. Their exceptional insulation homes decrease warm loss. Kilns get to target temperature levels faster while making use of much less power.
These rollers operate in oxidizing or decreasing environments. They execute reliably in different kiln settings. Their stability sustains precise temperature control. This is important for accomplishing uniform floor tile colors and textures. Producers avoid defects like warping or irregular shrinking.
The rollers require minimal maintenance. They stand up to thermal shock and rust from acidic fumes. This makes certain consistent procedure over hundreds of shooting cycles. Their lightweight style eases setup and handling. Production lines keep high throughput without disruptions.
Fused silica quartz ceramic rollers fulfill modern-day ceramic tile industry demands. They incorporate longevity, thermal efficiency, and cost-effectiveness. Manufacturing facilities accomplish greater outcome with less denies. The rollers’ dependability sustains constant kiln procedure. This makes them a functional upgrade for boosting floor tile production processes.
Company Introduction
Advanced Ceramics founded on October 17, 2014, is a high-tech enterprise committed to the research and development, production, processing, sales and technical services of ceramic relative materials and products.. Since its establishment in 2014, the company has been committed to providing customers with the best products and services, and has become a leader in the industry through continuous technological innovation and strict quality management.
Our products includes but not limited to Silicon carbide ceramic products, Boron Carbide Ceramic Products, Boron Nitride Ceramic Products, Silicon Carbide Ceramic Products, Silicon Nitride Ceramic Products, Zirconium Dioxide Ceramic Products, Quartz Products, etc. Please feel free to contact us.(nanotrun@yahoo.com)
Payment Methods
T/T, Western Union, Paypal, Credit Card etc.
Shipment Methods
By air, by sea, by express, as customers request.
5 FAQs of Fused Silica Quartz Ceramic Roller for Tile Kiln Furnace Ceramic Roller
Fused silica quartz ceramic rollers are used in tile kiln furnaces. They support and move tiles through high-temperature zones. Here are answers to common questions.
What materials are these rollers made of? They use fused silica and quartz. These materials are high-purity. They are melted and molded into roller shapes. This process creates strong, heat-resistant products.
Why pick fused silica rollers over metal ones? Metal rollers warp under extreme heat. Fused silica stays stable. It handles temperatures up to 1300°C. It resists thermal shock. Sudden temperature changes won’t crack it.
How do these rollers improve tile quality? They stay flat during firing. Tiles don’t bend or stick. The surface stays smooth. This reduces defects. Production consistency improves.
How long do fused silica rollers last? They outlast metal or standard ceramic rollers. Proper use extends their lifespan. They resist wear, corrosion, and chemical damage. Regular checks prevent unexpected breaks.
How to maintain these rollers? Clean them often. Remove dust or glaze buildup. Avoid rough handling. Store them in dry areas. Check for cracks or wear. Replace damaged rollers fast.
These rollers work in harsh conditions. They cut downtime. They boost kiln efficiency. Factories save money over time. Users report fewer production stops. Tile quality stays high.
(Fused Silica Quartz Ceramic Roller for Tile Kiln Furnace Ceramic Roller)
REQUEST A QUOTE
RELATED PRODUCTS
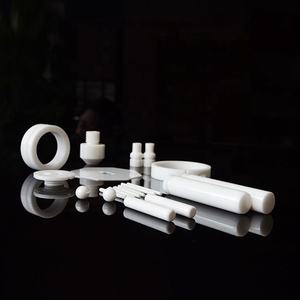
Melting Gold Platinum Fused Silica Quartz Ceramic Crucible Dish Bowl
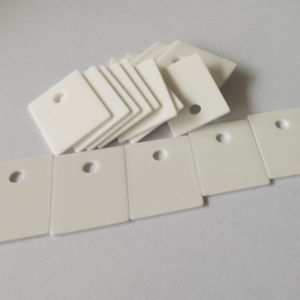
Whole Factory Supply of Natural Silica Quartz for Ferro Silicon Indian at Competitive Export
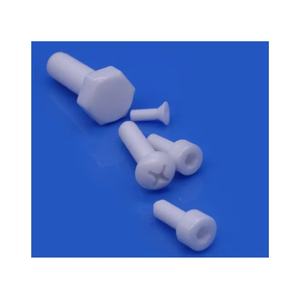
Fused Silica Quartz Crucible Casting Dish
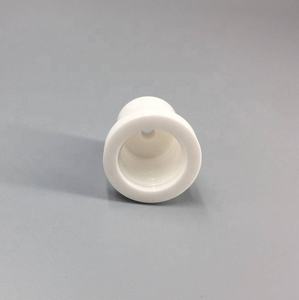
Beautiful Quartzite Stone Roma Imperial Quartzite for Countertop
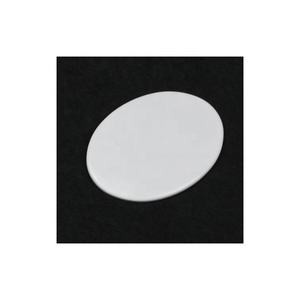
Factory Direct Best Quality Construction Fine Silica Sand Premium River and Sea Sand at Whole s Quartz Products
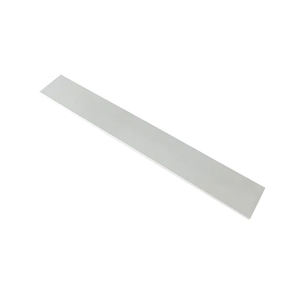