Discover Premium Ceramic Products | Durability & Elegance United | Advanced Ceramics
PRODUCT PARAMETERS
Description
Introduction to Quartz Ceramic Products
Quartz ceramic, also known as fused quartz ceramic or pure silicon ceramic, is an advanced ceramic material made of pure silicon dioxide (SiO₂). It is made by melting high-purity quartz sand at high temperature and then cooling and solidifying it. It has unique physical and chemical properties, making it an ideal choice for many high-tech applications. Quartz ceramic products are widely used in semiconductor manufacturing, optics, electronics, chemical industry and high-temperature industries.
Characteristics and advantages of quartz ceramics
Extremely high thermal stability: Quartz ceramics can remain stable under extreme temperature conditions. They are not only resistant to high temperatures, but also show excellent thermal shock resistance in rapid temperature changes.
Low thermal expansion coefficient: Due to its low thermal expansion coefficient, quartz ceramics have good dimensional stability when the temperature changes and are not easy to deform or crack.
Excellent electrical insulation: Provides excellent electrical insulation performance and is suitable for applications requiring high voltage isolation.
High transparency: It has good light transmittance in a wide band from ultraviolet to infrared, and is particularly suitable for applications such as optical windows and lenses.
Chemical stability: Excellent resistance to most acids, alkalis and other corrosive substances, and almost unaffected by other chemicals except hydrofluoric acid and phosphoric acid.
Mechanical strength: Although quartz ceramic is not as hard as some other types of ceramics, it still has enough mechanical strength to meet the needs of many application scenarios.
High UV transmittance: It has high transmittance in the ultraviolet region, which makes it very useful in UV curing equipment and UV spectrometers.
(Lower Quartz Powder Widely Use in Investment Casting)
Specifications of Lower Quartz Powder Widely Use in Investment Casting
Lower quartz powder works as a vital material in financial investment spreading. The item fulfills stringent high quality standards for commercial applications. It is made from high-purity quartz ore. The silica web content goes beyond 99.5%. This ensures marginal impurities. The powder’s particle dimension ranges between 200 mesh and 325 mesh. Consistent granules improve binding throughout mold development. The material’s reduced thermal growth stops splits under heats. This stability sustains specific spreading results.
The powder’s moisture content stays listed below 0.2%. Dry skin stays clear of undesirable responses in ceramic slurries. Its pH level stays neutral. This protects against rust in mold and mildews. The product’s angular fragment form enhances slurry thickness. Better viscosity permits also finish on wax patterns. The refractory homes stand up to temperatures above 1700 ° C. This makes sure mold and mildews hold shape during steel pouring.
Reduced quartz powder operates in multi-layer shell-building processes. It bonds well with binders like silica sol. The result is strong, smooth mold surface areas. Fine particles load gaps in ceramic layers. This minimizes flaws in final castings. The product works with zircon flour and alumina. Mixing improves shell toughness for intricate geometries.
The powder’s low alkali content reduces interaction with molten metals. This protects casting purity. It is chemically inert. Reactions with alloys are uncommon. The product suits stainless steel, superalloys, and titanium spreading. It leaves marginal residue after dewaxing. This cuts post-processing time.
Constant quality control checks consist of screen evaluation and X-ray fluorescence. Sets meet ASTM and ISO standards. The powder is packaged in moisture-proof bags. Storage space stays simple in dry settings. Individuals consist of aerospace, automotive, and tooling industries.
Reduced quartz powder improves covering longevity and dimensional accuracy. It lowers shell cracks and steel penetration. Expense performance comes from low waste prices. Reusing excess powder is possible. This sustains lasting foundry operations. The product’s integrity makes it a conventional choice for accuracy spreading.
(Lower Quartz Powder Widely Use in Investment Casting)
Applications of Lower Quartz Powder Widely Use in Investment Casting
Lower quartz powder plays a vital function in investment casting. This product is finely ground silica with high pureness. Its buildings make it ideal for producing accurate ceramic molds. These mold and mildews are made use of to produce metal parts with complex forms. Lower quartz powder is widely applied in the investment casting procedure for several factors.
The powder forms the base product for ceramic shells. It combines with binders to produce slurry. The slurry layers wax patterns layer by layer. This builds a strong mold and mildew around the wax. After drying, the wax thaws out. The staying ceramic shell becomes the mold for liquified steel. Lower quartz powder makes sure the covering stays secure throughout high-temperature putting.
An additional application is enhancing surface coating. The fine bits fill little gaps in the mold and mildew. This decreases roughness on the final steel component. It additionally helps capture complex information from the original pattern. Parts used this method require much less machining after casting. This conserves time and costs.
Thermal resistance is a significant benefit. Lower quartz powder deals with severe heat without cracking. This prevents problems like steel leak or mold and mildew breakage. It maintains the mold and mildew form constant until the steel cools. Regular mold and mildews imply fewer denied components.
The product is economical. It is cheaper than choices like zircon sand. It also needs much less binder product. This decreases general manufacturing expenses. Lots of foundries choose it for high-volume tasks.
Lower quartz powder works in other markets too. It is used in refractory products for steelmaking. It appears in ceramics and glass production. Some electronics producers utilize it for insulation parts. Its adaptability makes it important across manufacturing markets.
The powder’s bit size can be readjusted. This suits various casting requirements. Fine powders work for tiny, detailed components. Coarser grades deal with bigger elements. This adaptability meets varied client needs.
Handling the material is secure. It does not launch harmful dust. Employees can process it with fundamental safety equipment. Storage is easy. It stays secure in dry conditions.
Financial investment spreading depends on products that balance efficiency and cost. Lower quartz powder fulfills both needs. Its duty in creating high-grade steel components maintains it sought after. Producers remain to discover new usages for this versatile product.
Company Introduction
Advanced Ceramics founded on October 17, 2014, is a high-tech enterprise committed to the research and development, production, processing, sales and technical services of ceramic relative materials and products.. Since its establishment in 2014, the company has been committed to providing customers with the best products and services, and has become a leader in the industry through continuous technological innovation and strict quality management.
Our products includes but not limited to Silicon carbide ceramic products, Boron Carbide Ceramic Products, Boron Nitride Ceramic Products, Silicon Carbide Ceramic Products, Silicon Nitride Ceramic Products, Zirconium Dioxide Ceramic Products, Quartz Products, etc. Please feel free to contact us.(nanotrun@yahoo.com)
Payment Methods
T/T, Western Union, Paypal, Credit Card etc.
Shipment Methods
By air, by sea, by express, as customers request.
5 FAQs of Lower Quartz Powder Widely Use in Investment Casting
Lower quartz powder is a key material in investment casting. Here are five common questions about its use. What is lower quartz powder? It is a fine-ground material made from high-purity quartz. It has high heat resistance and chemical stability. This makes it ideal for creating ceramic shells in casting. Why is it used in investment casting? The powder forms strong ceramic layers when mixed with binders. These layers withstand extreme temperatures during metal pouring. They also break away cleanly after cooling. This leaves precise metal parts. What benefits does it offer over other materials? Lower quartz powder improves shell durability. It reduces cracks or distortions in final products. It ensures consistent surface finishes. This saves time and costs in post-processing. How does particle size affect performance? Smaller particles create smoother shell surfaces. Larger particles add strength to thicker layers. Manufacturers adjust particle sizes based on mold complexity. This balances detail and structural integrity. Are there safety concerns with handling? The powder is safe if handled properly. Workers should wear masks to avoid inhaling fine dust. Proper ventilation in workspaces minimizes airborne particles. Storage in dry conditions prevents clumping or contamination. Lower quartz powder remains a reliable choice for precision casting applications.
(Lower Quartz Powder Widely Use in Investment Casting)
REQUEST A QUOTE
RELATED PRODUCTS
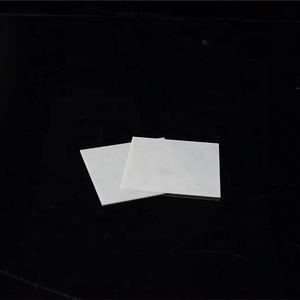
Factory Quartz Limestone Coal Ceramic Cement Dry Grinding Mill Machine, Industrial Wet Gold Ore Mining Ball Mill for
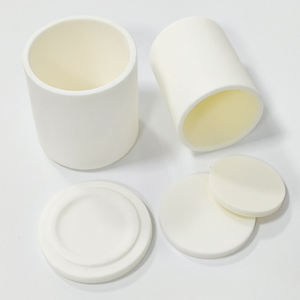
Factory Direct s of High Temperature Resistant Transparent Quartz Glass Sheets
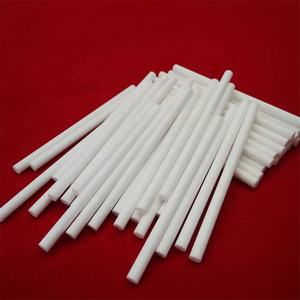
Low on High Purity Natural Quartz Powder for Glass Making Industries Buy at Lowest
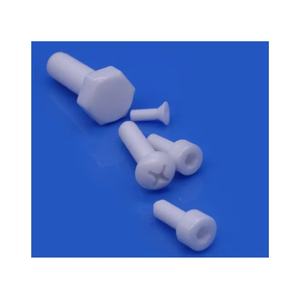
Fused Silica Quartz Crucible Casting Dish
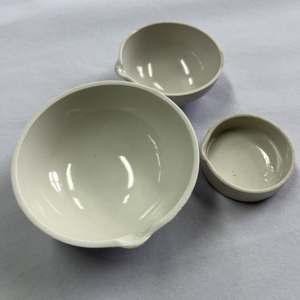
High Grade Quartz Available at Whole
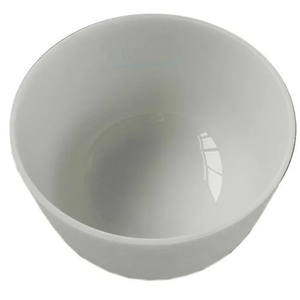