Discover Premium Ceramic Products | Durability & Elegance United | Advanced Ceramics
PRODUCT PARAMETERS
Description
Overview of Silicon Carbide Ceramics
Silicon Carbide (SiC) ceramics are renowned for their outstanding mechanical properties, including high hardness, strength at elevated temperatures, and excellent thermal shock resistance. These materials are pivotal in cutting-edge industrial applications, from abrasives to aerospace components, due to their unique combination of properties.
Features of Silicon Carbide Ceramics
High Hardness: Exceptional wear resistance.
Thermal Shock Resistance: Can withstand rapid temperature changes.
Chemical Stability: Resistant to most chemicals.
High Thermal Conductivity: Efficient heat dissipation.
Low Density: Lightweight for its strength.
(OEM Customized Refractory Material Ceramic Sintered Silicon Carbide burner Nozzles Sic Flame Tube Sleeve for Furnace)
Specification of OEM Customized Refractory Material Ceramic Sintered Silicon Carbide burner Nozzles Sic Flame Tube Sleeve for Furnace
Specification of OEM Customized Refractory Product Porcelain Sintered Silicon Carbide Burner Nozzles SiC Flame Tube Sleeve for Furnace. These burner nozzles are developed for high-temperature commercial heating system applications. They are made from sintered silicon carbide, a product known for remarkable thermal conductivity, mechanical toughness, and resistance to thermal shock. The item endures extreme temperatures approximately 1650 ° C in oxidizing or corrosive atmospheres. Customization alternatives guarantee compatibility with particular heater designs.
The nozzles include exact dimensions customized to client needs. Typical sizes range from 20mm to 300mm in size, with sizes flexible based on furnace arrangements. The product’s low thermal growth reduces splitting under rapid temperature level adjustments. This sturdiness lowers downtime caused by frequent substitutes.
Secret technical requirements consist of a thickness of 3.0-3.2 g/cm SIX, guaranteeing architectural stability under lots. The porosity is regulated below 15% to stop gas penetration and preserve surface area integrity. Compressive stamina surpasses 350 MPa, permitting the nozzles to handle mechanical tension in high-pressure heater zones. Surface area coating alternatives are offered to maximize flame distribution and combustion efficiency.
These SiC components stand up to chemical deterioration from acids, antacid, and molten steels. They are optimal for industries like metallurgy, porcelains, and chemical handling. The non-reactive nature of silicon carbide guarantees constant performance in aggressive environments. Installment is uncomplicated because of standardized threading or flange designs. Upkeep requirements are very little, lowering functional prices in time.
Customized burner nozzles sustain gas kinds including gas, oil, and powdered coal. They boost combustion harmony, decreasing energy waste. The item’s high thermal conductivity boosts heat transfer prices, boosting furnace efficiency. Compatibility with automated control systems allows seamless integration into modern-day commercial configurations.
Quality control includes rigorous screening for dimensional precision and material purity. Production adheres to ISO and ASTM criteria to ensure integrity. Lead times vary based on design intricacy, with mass orders focused on for large-scale jobs. Technical support is offered for installment support and performance optimization.
Applications span steelmaking, glass production, waste incineration, and warm treatment heating systems. The nozzles excel in settings where traditional materials fail due to thermal exhaustion. Personalized designs accommodate special burner formats or space restrictions. Replacement routines are predictable, streamlining inventory management for plant operators.
The item is packaged securely to prevent damage throughout delivery. Custom branding or classifying choices are provided for OEM partners. Examples can be provided for initial testing before major fostering. Rates shows order volume and personalization levels, with discount rates for lasting contracts.
(OEM Customized Refractory Material Ceramic Sintered Silicon Carbide burner Nozzles Sic Flame Tube Sleeve for Furnace)
Applications of OEM Customized Refractory Material Ceramic Sintered Silicon Carbide burner Nozzles Sic Flame Tube Sleeve for Furnace
OEM tailored refractory material ceramic sintered silicon carbide (SiC) burner nozzles and SiC fire tube sleeves are necessary elements in high-temperature industrial heating system systems. These items are made for extreme settings. They deal with intense warmth, chemical direct exposure, mechanical stress and anxiety. Industries like metallurgy, chemical processing, glass manufacturing, porcelains count on them for reliable operations.
The key use SiC heater nozzles is guiding and regulating fuel combustion in heaters. Their high thermal conductivity guarantees even warmth circulation. This protects against locations. It expands equipment lifespan. The material stands up to oxidation, corrosion. It keeps architectural honesty at temperatures above 1600 ° C. This makes it ideal for long term usage in extreme problems.
SiC flame tube sleeves shield furnace insides from direct flame contact. They decrease endure furnace walls. This lowers upkeep costs. Their low thermal development coefficient stops splitting under rapid temperature changes. Factories utilizing these sleeves report less closures. Manufacturing continuity boosts.
Modification is an essential benefit. Suppliers tailor dimensions, shapes, density to fit specific heating system layouts. This makes sure smooth integration. Nozzles and sleeves function efficiently with existing configurations. Customized creates address one-of-a-kind challenges like irregular furnace geometries or unusual fuel types.
The ceramic sintered silicon carbide product offers exceptional sturdiness. It surpasses conventional materials like alumina or zirconia. It stands up to abrasion from particle matter in fuel streams. This minimizes disintegration gradually. Energy effectiveness boosts. Gas intake decreases because of specific flame control.
These components are critical in glass melting furnaces. They endure molten glass sprinkles, alkali vapors. In steel warm therapy, they sustain molten metal splatter. Chemical plants use them in reactors calling for corrosion-resistant parts.
Installation is straightforward. The lightweight nature of SiC streamlines handling. It decreases labor costs. Compatibility with conventional securing materials guarantees leak-free operation. Users change parts much less regularly. Downtime reduces.
Performance uniformity is ensured. Rigorous quality checks test thermal shock resistance, thickness, porosity. Each unit meets industry standards. Makers supply technological assistance for repairing. They help choose the appropriate specs for details applications.
The mix of personalization, resilience, thermal stability makes these SiC items important for modern-day industrial home heating procedures. They boost safety and security, effectiveness, cost-effectiveness across several markets.
Company Introduction
Advanced Ceramics founded on October 17, 2014, is a high-tech enterprise committed to the research and development, production, processing, sales and technical services of ceramic relative materials and products.. Since its establishment in 2014, the company has been committed to providing customers with the best products and services, and has become a leader in the industry through continuous technological innovation and strict quality management.
Our products includes but not limited to Silicon carbide ceramic products, Boron Carbide Ceramic Products, Boron Nitride Ceramic Products, Silicon Carbide Ceramic Products, Silicon Nitride Ceramic Products, Zirconium Dioxide Ceramic Products, Quartz Products, etc. Please feel free to contact us.(nanotrun@yahoo.com)
Payment Methods
T/T, Western Union, Paypal, Credit Card etc.
Shipment Methods
By air, by sea, by express, as customers request.
5 FAQs of OEM Customized Refractory Material Ceramic Sintered Silicon Carbide burner Nozzles Sic Flame Tube Sleeve for Furnace
Silicon carbide burner nozzles handle extreme heat. They last longer than metal or ceramic options. Their high thermal conductivity spreads heat evenly. This prevents hot spots. It reduces damage risk in furnace operations.
Custom sizes and shapes are available. Manufacturers provide drawings or specs. Production teams create samples for approval. Adjustments ensure fit for specific furnace setups. OEM services support unique project needs.
These nozzles withstand temperatures up to 1600°C. They resist thermal shock from rapid heating or cooling. Chemical corrosion from gases or molten materials is less likely. This makes them reliable in harsh industrial environments.
Installation works with standard furnace systems. Compatibility depends on flange designs or mounting methods. Custom nozzles may need modified setups. Users should confirm measurements before ordering. Professional installation avoids alignment issues.
Maintenance involves checking for cracks or wear. Regular cleaning removes debris blocking fuel flow. Lifespan varies with operating conditions. High-temperature cycles or abrasive materials may shorten it. Inspections every six months help spot early damage. Replacements prevent unexpected downtime.
(OEM Customized Refractory Material Ceramic Sintered Silicon Carbide burner Nozzles Sic Flame Tube Sleeve for Furnace)
REQUEST A QUOTE
RELATED PRODUCTS
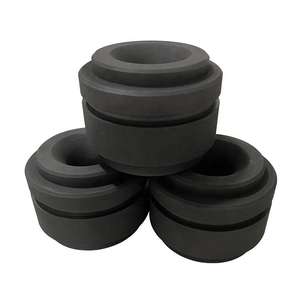
Refractory Silicon Carbide Ceramic SSIC Tube Sic Tube Protect Tube
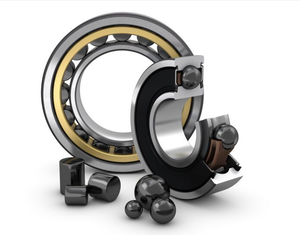
Customized Refractory Silicon Carbide Plate Silicon Carbide Ceramic Plates For Industrial Furnace
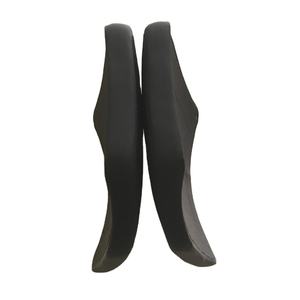
Durable Silicon Carbide Ceramic Sealing Ring Premium Product in Seals Category
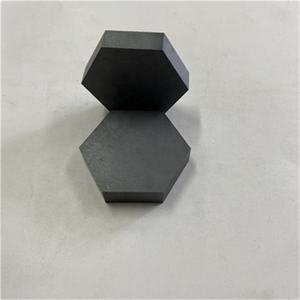
High Quality Refractory Silicon Carbide Sic Carbide Ceramic Plate Sinter Reaction Plate
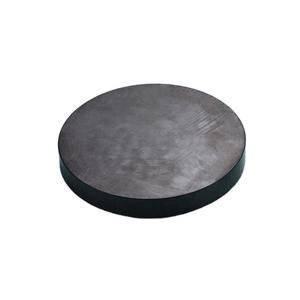
Factory SSIC Sintered Silicon Carbide SIC Bushing Ceramic Lining Axle Shaft Sleeve for Magnetic Pump
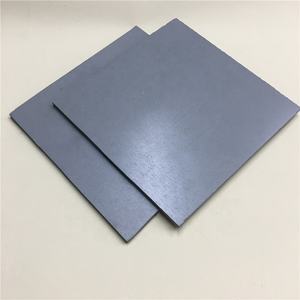