Discover Premium Ceramic Products | Durability & Elegance United | Advanced Ceramics
PRODUCT PARAMETERS
Description
Overview of Silicon Nitride Ceramics
Silicon Nitride Ceramics are high-performance materials known for their excellent mechanical properties, including strength, toughness, and resistance to wear, corrosion, and thermal shock, making them ideal for demanding applications in various industries.
Features of Silicon Nitride Ceramics
Exceptional hardness and wear resistance.
Superior mechanical strength and fracture toughness.
Excellent thermal stability and resistance to thermal shock.
High corrosion resistance in aggressive environments.
Low density contributing to lightweight components.
(CNC machining Silicon nitride/Si3N4 ceramic parts)
Specifications of CNC machining Silicon nitride/Si3N4 ceramic parts
CNC machining silicon nitride (Si3N4) ceramic parts includes generating high-performance elements for demanding commercial applications. Silicon nitride ceramic is known for its exceptional mechanical toughness. It withstands thermal shock, runs reliably in severe temperatures, and maintains stability in settings as much as 1200 ° C. The product’s reduced density reduces part weight while supplying firmness similar to industrial-grade steel. Electrical insulation homes make it suitable for electronic devices. Chemical resistance allows use in destructive settings like chemical processing equipment.
Accuracy CNC machining makes certain tight resistances, generally within ± 0.01 mm. Advanced tools like diamond-coated cutters deal with the ceramic’s firmness. Facility geometries are possible, consisting of thin wall surfaces, complex networks, and great threads. Surface surfaces vary from Ra 0.2 μm for sleek choices to Ra 1.6 μm for standard components. Post-processing choices like grinding or lapping boost dimensional accuracy.
Silicon nitride parts suit markets requiring longevity under stress and anxiety. Aerospace applications include turbine blades and bearings. Automotive systems utilize them in engine parts and sensing units. Medical gadgets take advantage of biocompatibility and put on resistance. Semiconductor producing counts on silicon nitride for wafer handling and insulation.
Modification covers dimensions from millimeters to over 500 mm in size. Models and mass production are supported. Material grades vary, with choices maximized for thermal conductivity or fracture sturdiness. Quality assurance includes dimensional checks, surface area inspection, and performance testing. X-ray or ultrasound techniques find interior flaws.
Machining silicon nitride needs experience due to brittleness. Appropriate device courses and cooling avoid cracking. Knowledgeable suppliers reduce product waste. Expense performance enhances with batch production. Lead times depend on part intricacy, normally varying from days to weeks.
Silicon nitride’s mix of toughness, thermal stability, and deterioration resistance makes it a top selection for essential applications. Appropriate machining ensures parts meet rigorous industry criteria.
(CNC machining Silicon nitride/Si3N4 ceramic parts)
Applications of CNC machining Silicon nitride/Si3N4 ceramic parts
CNC machining silicon nitride (Si3N4) ceramic components makes it possible for high accuracy in markets requiring severe toughness and thermal security. These components handle rough settings because of their resistance to use, warmth, and corrosion. Aerospace applications utilize Si3N4 components like turbine blades and bearings. The product’s low weight and strength boost gas efficiency and performance in jet engines. High-speed cutting tools made from silicon nitride last longer than steel choices. They reduce downtime in manufacturing processes. Automotive systems benefit from Si3N4 parts in engines and exhausts. The ceramic withstands high temperatures without weakening. This boosts integrity in elements like glow plugs and sensing units. Electric lorries make use of these ceramics for battery insulation and thermal monitoring. Medical gadgets count on silicon nitride for implants and medical devices. Its biocompatibility prevents adverse reactions in the body. CNC machining makes certain limited resistances for joint substitutes and dental prosthetics. The material’s smooth surface area lowers bacterial development. Electronics manufacturers make use of Si3N4 substratums and insulators. The ceramic’s electric insulation buildings protect circuits in high-voltage atmospheres. Warmth sinks made from silicon nitride take care of thermal loads in power modules. Commercial equipment integrates Si3N4 components for wear-resistant linings and seals. The ceramic’s firmness prolongs the lifespan of pumps and valves in abrasive problems. Chemical handling plants utilize these parts to stand up to harsh materials. Silicon nitride’s thermal shock resistance fits quick temperature changes in furnaces. CNC machining allows complicated forms for personalized applications. This adaptability supports prototyping and automation. The process accomplishes fine information without endangering architectural integrity. Surface area finishes fulfill rigorous requirements for friction-sensitive parts. Silicon nitride porcelains operate in vacuum environments for semiconductor manufacturing. Their reduced thermal development ensures stability in accuracy optics and laser systems. Food handling equipment makes use of Si3N4 parts for non-reactive surfaces. The product fulfills hygiene demands while dealing with acidic active ingredients. Renewable resource systems use these ceramics in wind generator bearings. They endure variable tons and reduce upkeep costs.
Company Introduction
Advanced Ceramics founded on October 17, 2014, is a high-tech enterprise committed to the research and development, production, processing, sales and technical services of ceramic relative materials and products.. Since its establishment in 2014, the company has been committed to providing customers with the best products and services, and has become a leader in the industry through continuous technological innovation and strict quality management.
Our products includes but not limited to Silicon carbide ceramic products, Boron Carbide Ceramic Products, Boron Nitride Ceramic Products, Silicon Carbide Ceramic Products, Silicon Nitride Ceramic Products, Zirconium Dioxide Ceramic Products, Quartz Products, etc. Please feel free to contact us.(nanotrun@yahoo.com)
Payment Methods
T/T, Western Union, Paypal, Credit Card etc.
Shipment Methods
By air, by sea, by express, as customers request.
5 FAQs of CNC machining Silicon nitride/Si3N4 ceramic parts
1. What is CNC machining for silicon nitride ceramic parts?
CNC machining shapes silicon nitride parts using computer-controlled tools. The process removes material from a solid block to create precise components. Silicon nitride is extremely hard. Specialized diamond-coated tools are needed. This method works for complex geometries. It suits industries needing high-performance ceramics.
2. Why choose silicon nitride for CNC machining?
Silicon nitride resists heat, wear, and corrosion better than metals. It performs well in extreme environments. The material is lightweight. It has high strength. These properties make it ideal for aerospace, automotive, and medical applications. CNC machining ensures tight tolerances for critical parts.
3. What challenges exist in CNC machining silicon nitride?
The material’s hardness causes rapid tool wear. Brittle nature raises cracking risks. Machining requires slow speeds. Special cooling methods prevent overheating. Experienced operators adjust parameters carefully. Costs are higher than machining metals. Proper tool selection minimizes defects.
4. What tolerances are achievable with CNC-machined silicon nitride?
Tolerances depend on part size and design. Standard precision reaches ±0.01 mm. Advanced setups achieve tighter tolerances. Surface finishes improve with polishing. Complex shapes need multiple machining steps. Consistency relies on machine calibration. Quality checks ensure specifications are met.
5. How does CNC machining cost compare for silicon nitride vs. metals?
Silicon nitride costs more to machine. Material prices are higher. Tooling expenses increase due to diamond tools. Longer machining times add labor costs. Benefits like durability and performance justify the investment. Small batches cost more per unit. Larger orders reduce per-part expenses.
(CNC machining Silicon nitride/Si3N4 ceramic parts)
REQUEST A QUOTE
RELATED PRODUCTS
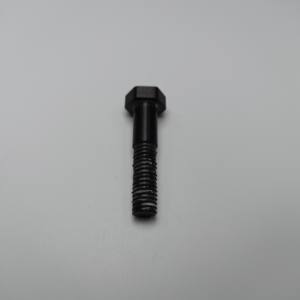
0.4mm-100mm G5-G40 Ceramic Balls Silicon Nitride Ball Si3n4 For Bearings Sealing Special Ball
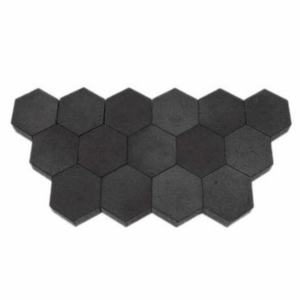
Best of Silicon Nitride Powder High Purity Si3N4 Silicon Nitride CAS 12033-89-5 for Ceramic Abrasive Industry
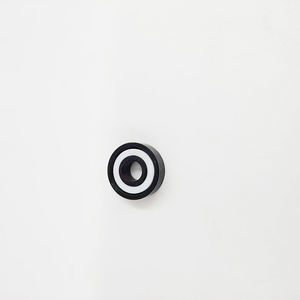
Si3N4 Customized High Quality Silicon Nitride Ceramic Nozzle for Welding
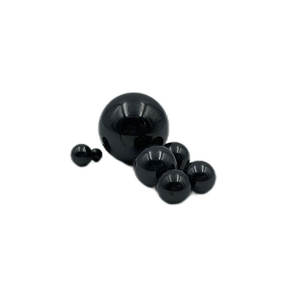
High Wear Resistant Gas Silicon Nitride Ceramic Ring
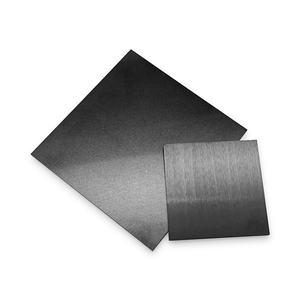
Diamond multi-wire cutting equipment for sapphire special ceramics and silicon nitride
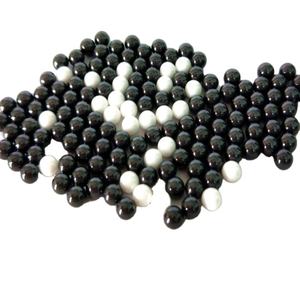