Discover Premium Ceramic Products | Durability & Elegance United | Advanced Ceramics
PRODUCT PARAMETERS
Description
Overview of Silicon Nitride Ceramics
Silicon Nitride Ceramics are high-performance materials known for their excellent mechanical properties, including strength, toughness, and resistance to wear, corrosion, and thermal shock, making them ideal for demanding applications in various industries.
Features of Silicon Nitride Ceramics
Exceptional hardness and wear resistance.
Superior mechanical strength and fracture toughness.
Excellent thermal stability and resistance to thermal shock.
High corrosion resistance in aggressive environments.
Low density contributing to lightweight components.
(High Hardness Black Si3n4 Silicon Nitride Ceramic Insert/Cutter/Blade)
Specifications of High Hardness Black Si3n4 Silicon Nitride Ceramic Insert/Cutter/Blade
High Firmness Black Si3N4 Silicon Nitride Ceramic Inserts/Cutters/Blades supply innovative efficiency for requiring commercial applications. These components are crafted for severe toughness. The product incorporates high firmness with exceptional fracture sturdiness. It stands up to wear efficiently in high-stress settings.
Silicon nitride porcelains master thermal stability. They maintain strength at temperature levels as much as 1200 ° C. Thermal shock resistance avoids fracturing under fast temperature adjustments. This makes them optimal for high-speed machining.
The black Si3N4 variant features improved thickness. A fine-grained framework lowers surface defects. This improves side retention for reducing devices. The product’s low thermal growth reduces dimensional modifications throughout procedure. Consistent accuracy is attained over extended periods.
Chemical inertness enables usage in harsh environments. Acids and alkalis do not break down the ceramic. Oxidation resistance guarantees stability in oxygen-rich setups. This prolongs service life contrasted to metal choices.
Mechanical properties include a hardness of HRA 92-94. Compressive stamina surpasses 3000 MPa. The thickness varies from 3.2 to 3.3 g/cm ³. These characteristics decrease tool wear during heavy cutting. Machining efficiency increases with lowered downtime.
Applications cover metalworking, aerospace, and auto markets. The inserts take care of cast iron, nickel alloys, and set steels. Blades suit unpleasant products like composites or porcelains. High-speed reducing gain from decreased friction and heat generation.
Surface area surfaces are precision-ground for tight tolerances. Personalized geometries fit details machining demands. Coatings like TiN or Al2O3 improve performance even more. Compatibility with standard device holders streamlines combination.
Electric insulation buildings prevent existing leak. This suits applications requiring non-conductive tools. The product’s light-weight nature reduces machine tons. Power intake decreases throughout long term usage.
Manufacturing makes use of warm pushing or sintering methods. Quality assurance makes certain minimal porosity. Each batch undertakes strenuous screening for uniformity. Integrity meets ISO and sector standards.
Long-term cost savings result from lowered substitute frequency. Efficiency security decreases functional risks. These porcelains attend to challenges in modern production.
(High Hardness Black Si3n4 Silicon Nitride Ceramic Insert/Cutter/Blade)
Applications of High Hardness Black Si3n4 Silicon Nitride Ceramic Insert/Cutter/Blade
High solidity black Si3N4 silicon nitride ceramic inserts, cutters, and blades are crafted for requiring industrial applications. These parts master extreme problems because of their remarkable wear resistance, thermal security, and mechanical strength. They exceed traditional steel or carbide devices in high-speed, high-temperature atmospheres.
In metal machining, silicon nitride ceramic tools manage hard materials like actors iron, nickel alloys, and solidified steels. They decrease tool wear and maintain accuracy during transforming, milling, or grinding. The low thermal growth of silicon nitride stops deformation under heat, making sure constant efficiency. These devices also decrease friction, decreasing energy intake and extending service life.
Aerospace and vehicle markets depend on silicon nitride ceramic blades for reducing composite materials and heat-resistant alloys. Their resistance to oxidation and thermal shock makes them ideal for high-temperature processes. Turbine blade machining and engine component fabrication take advantage of their ability to hold up against fast temperature modifications without fracturing.
In food handling, silicon nitride cutters slice abrasive or sticky products without contamination. The non-reactive surface protects against chemical interactions, meeting health requirements. These blades stay sharp longer, minimizing downtime for substitutes.
Clinical device manufacturing makes use of silicon nitride parts for precision cutting of implants or medical tools. The product’s biocompatibility and resistance to sterilization procedures guarantee reliability in important applications.
Electronic devices manufacturing utilizes these porcelains for dicing semiconductor wafers or trimming circuit boards. The firmness of silicon nitride enables clean cuts without damaging delicate products. Electric insulation residential properties stop damage to sensitive parts.
Silicon nitride ceramic inserts are also used in woodworking and glass handling. They supply smooth finishes on breakable materials while standing up to rough wear. The combination of strength and lightweight design enhances taking care of efficiency.
These ceramic tools operate effectively in harsh atmospheres, such as chemical processing or aquatic applications. Resistance to acids and alkalis makes sure sturdiness where metals weaken swiftly. Customized shapes and sizes adapt to specialized machinery, supporting diverse industrial requirements.
Company Introduction
Advanced Ceramics founded on October 17, 2014, is a high-tech enterprise committed to the research and development, production, processing, sales and technical services of ceramic relative materials and products.. Since its establishment in 2014, the company has been committed to providing customers with the best products and services, and has become a leader in the industry through continuous technological innovation and strict quality management.
Our products includes but not limited to Silicon carbide ceramic products, Boron Carbide Ceramic Products, Boron Nitride Ceramic Products, Silicon Carbide Ceramic Products, Silicon Nitride Ceramic Products, Zirconium Dioxide Ceramic Products, Quartz Products, etc. Please feel free to contact us.(nanotrun@yahoo.com)
Payment Methods
T/T, Western Union, Paypal, Credit Card etc.
Shipment Methods
By air, by sea, by express, as customers request.
5 FAQs of High Hardness Black Si3n4 Silicon Nitride Ceramic Insert/Cutter/Blade
What is silicon nitride ceramic?
Silicon nitride ceramic is a synthetic material. It combines silicon and nitrogen. It has high hardness and heat resistance. It works well in extreme conditions. It lasts longer than metals or other ceramics in tough applications.
Why choose silicon nitride inserts over metal tools?
Silicon nitride stays hard at high temperatures. Metals soften when hot. This ceramic resists wear better. It cuts faster and lasts longer. It reduces downtime for tool changes. It saves money over time.
What applications suit silicon nitride blades?
These blades cut hard materials. Examples include cast iron, nickel alloys, and aerospace metals. They work in machining, grinding, and high-speed cutting. They handle high heat without cracking. They fit industries like automotive and manufacturing.
How to maintain silicon nitride cutters?
Clean them after use. Avoid sudden temperature changes. Store them dry to prevent moisture damage. Check for chips or cracks regularly. Replace damaged tools quickly. Proper care extends their lifespan.
Is silicon nitride ceramic cost-effective?
The initial cost is higher than steel. The durability makes up for it. Fewer replacements are needed. Productivity improves with faster cutting speeds. Long-term savings outweigh the upfront price. It works for heavy-duty or precision tasks.
(High Hardness Black Si3n4 Silicon Nitride Ceramic Insert/Cutter/Blade)
REQUEST A QUOTE
RELATED PRODUCTS
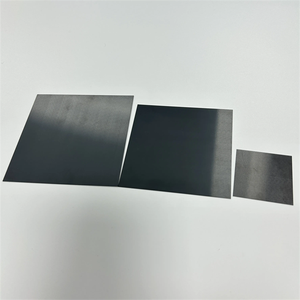
G5 G10 Class Si3N4 Silicon Nitride Ceramic Balls Balls 38mm with Silicon Nitride
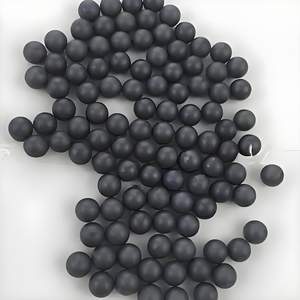
G5 G10 Si3N4 Silicon Nitride Ceramic Balls Balls Ceramic Grinding Ball with Silicon Nitride for Bearing
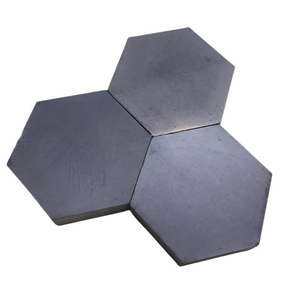
Si3N4 Ceramic Super Grinding Silicon Nitride Balls 3mm 4mm 5mm 10mm Nitrided Silicon Ceramic Ball
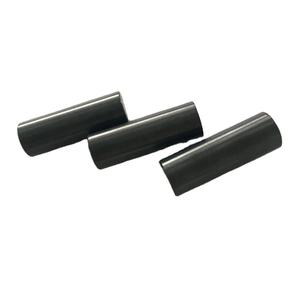
Silicon Nitride Ceramic Tube SiC Riser Tube for Thermocouple protection
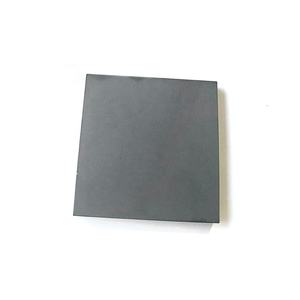
Heat-Resistant High Quality Precision Silicon Nitride Si3N4 Ceramic Part Roller Component
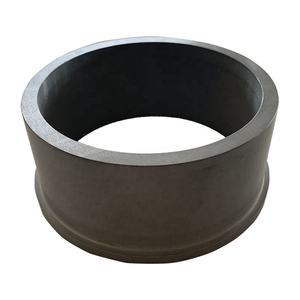