Discover Premium Ceramic Products | Durability & Elegance United | Advanced Ceramics
PRODUCT PARAMETERS
Description
Overview of Silicon Nitride Ceramics
Silicon Nitride Ceramics are high-performance materials known for their excellent mechanical properties, including strength, toughness, and resistance to wear, corrosion, and thermal shock, making them ideal for demanding applications in various industries.
Features of Silicon Nitride Ceramics
Exceptional hardness and wear resistance.
Superior mechanical strength and fracture toughness.
Excellent thermal stability and resistance to thermal shock.
High corrosion resistance in aggressive environments.
Low density contributing to lightweight components.
(Si3N4 Alumina Industrial Ceramic Substrate Wear Resistance Silicon Nitride Material for Structure Ceramic Parts)
Specifications of Si3N4 Alumina Industrial Ceramic Substrate Wear Resistance Silicon Nitride Material for Structure Ceramic Parts
Si3N4 alumina commercial ceramic substrate is a high-performance product designed for requiring applications. It combines silicon nitride and alumina to deliver outstanding wear resistance. This makes it suitable for parts subjected to rubbing and unpleasant atmospheres. The product has a high firmness level. It reaches up to 90 HRA on the Rockwell scale. This makes certain long-lasting efficiency also under hefty usage.
The ceramic substrate manages severe temperatures well. It runs accurately in settings ranging from -200 ° C to 1200 ° C. Thermal shock resistance is a key attribute. Rapid temperature modifications do not trigger cracking or destruction. This security is critical in sectors like aerospace and auto manufacturing.
Mechanical strength is one more benefit. The material’s flexural stamina exceeds 800 MPa. It stands up to bending or breaking under hefty lots. This resilience sustains structural stability in high-stress components. Chemical resistance is also strong. Acids, antacid, and corrosive gases do not harm the substrate. This makes it optimal for chemical processing equipment.
Surface area smoothness is enhanced for accuracy applications. The reduced rubbing coefficient lowers power loss in relocating parts. This boosts effectiveness in equipment like bearings and seals. Electrical insulation properties are outstanding. The material protects against existing leak in high-voltage settings. This is useful in electronics and power transmission systems.
Modification options are available. The substrate can be machined right into complicated shapes. Tolerances as limited as ± 0.01 mm satisfy stringent design requirements. It works with finishes or metallization for boosted capability.
Applications cover multiple markets. Automotive systems use it for engine elements and sensors. Semiconductor making relies upon it for wafer-handling parts. Industrial equipment integrates it for wear-resistant linings and guides. Medical gadgets benefit from its biocompatibility and sterilizability.
The material fulfills worldwide top quality criteria. It undergoes extensive testing for density, porosity, and microstructure. Regular efficiency is guaranteed throughout manufacturing sets. This reliability minimizes downtime and maintenance costs in commercial procedures.
Si3N4 alumina ceramic substratum offers a cost-efficient solution for high-wear applications. Its mix of physical, thermal, and chemical properties ensures adaptability. Industries prioritize it for critical elements calling for precision and toughness.
(Si3N4 Alumina Industrial Ceramic Substrate Wear Resistance Silicon Nitride Material for Structure Ceramic Parts)
Applications of Si3N4 Alumina Industrial Ceramic Substrate Wear Resistance Silicon Nitride Material for Structure Ceramic Parts
Silicon nitride (Si3N4) alumina industrial ceramic substratums are advanced products utilized commonly in high-performance applications. These substrates combine silicon nitride’s toughness with alumina’s thermal stability. They work well in settings requiring wear resistance, thermal shock resistance, and mechanical durability. Their structure makes them suitable for components revealed to extreme problems.
In electronic devices, Si3N4 alumina substratums act as base materials for circuits. They manage warm successfully in power components and LED systems. Their low thermal development avoids breaking under temperature level changes. This dependability ensures longer-lasting electronic elements.
Aerospace and auto industries utilize these porcelains for engine parts and sensors. Silicon nitride takes care of high heat and friction in wind turbine blades and bearings. It minimizes wear in relocating components. Alumina adds corrosion resistance against chemicals and dampness. This mix prolongs component life times in harsh setups.
Industrial machinery relies on Si3N4 alumina for cutting devices and nozzles. The product’s hardness withstands abrasion during machining or product handling. It preserves shape under hefty loads. This minimizes downtime from part replacements.
Power markets use these porcelains in solar panels and atomic power plants. They protect electrical systems while sustaining radiation or high temperatures. Their stability supports constant performance in renewable resource configurations.
Clinical devices utilizes silicon nitride alumina composites for implants and surgical devices. The material’s biocompatibility avoids negative reactions in the body. Its smooth surface area reduces wear in joint replacements.
Makers choose Si3N4 alumina substratums for personalized architectural ceramic parts. Alternatives consist of machining pre-sintered blanks or finishing fully densified porcelains. The process makes certain accurate measurements for limited resistances.
These ceramics fit applications needing lightweight yet tough products. They exceed steels in high-stress scenarios. Their resistance to oxidation and thermal biking makes them economical in time.
Silicon nitride alumina substratums meet needs throughout sectors requiring dependability under stress. Their versatility to various production methods enables customized solutions. This adaptability sustains technology in engineering and innovation.
Company Introduction
Advanced Ceramics founded on October 17, 2014, is a high-tech enterprise committed to the research and development, production, processing, sales and technical services of ceramic relative materials and products.. Since its establishment in 2014, the company has been committed to providing customers with the best products and services, and has become a leader in the industry through continuous technological innovation and strict quality management.
Our products includes but not limited to Silicon carbide ceramic products, Boron Carbide Ceramic Products, Boron Nitride Ceramic Products, Silicon Carbide Ceramic Products, Silicon Nitride Ceramic Products, Zirconium Dioxide Ceramic Products, Quartz Products, etc. Please feel free to contact us.(nanotrun@yahoo.com)
Payment Methods
T/T, Western Union, Paypal, Credit Card etc.
Shipment Methods
By air, by sea, by express, as customers request.
5 FAQs of Si3N4 Alumina Industrial Ceramic Substrate Wear Resistance Silicon Nitride Material for Structure Ceramic Parts
Si3N4 alumina industrial ceramic substrate is a high-performance material combining silicon nitride and alumina. It is designed for structural ceramic parts requiring extreme durability. Below are answers to common questions.
What is Si3N4 alumina industrial ceramic substrate?
This material blends silicon nitride with alumina. It offers high strength, thermal stability, and resistance to wear. It is used in harsh environments like high-temperature machinery or abrasive conditions.
Why is Si3N4 alumina ceramic ideal for wear resistance?
The material has a dense structure. It resists scratches, erosion, and surface degradation. Its hardness reduces friction, extending component lifespan in high-stress applications.
Where is this ceramic substrate typically applied?
It is used in industrial machinery, cutting tools, bearings, and engine components. Electronics use it for insulating substrates. Its stability suits aerospace, automotive, and manufacturing sectors.
How should Si3N4 alumina ceramic be machined?
Diamond-tipped tools are required. Standard tools wear quickly. Machining must be slow to prevent cracking. Proper cooling and secure clamping reduce vibration damage.
Does Si3N4 alumina ceramic cost more than other materials?
Initial costs are higher than metals or plastics. Long-term savings come from reduced replacements. It outperforms alternatives in extreme conditions, lowering downtime and maintenance.
(Si3N4 Alumina Industrial Ceramic Substrate Wear Resistance Silicon Nitride Material for Structure Ceramic Parts)
REQUEST A QUOTE
RELATED PRODUCTS
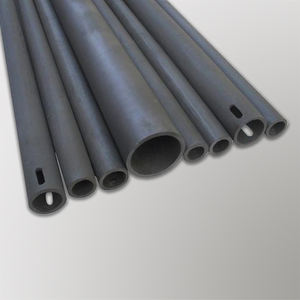
Industrial Ceramic Si3N4 Silicon Nitride Disc Plate Parts Zirconia Material Included Moulding Service for Grinding Applications
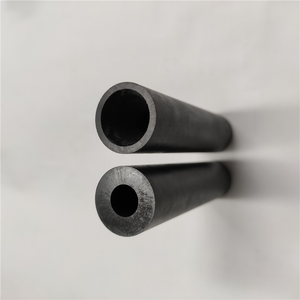
Custom High Hard Strong Gas Pressure Sintering Silicon Nitride Ceramic Part Si3N4 Piece with Hole
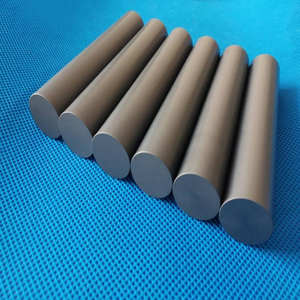
High Purity Si3N4 Micron Powder Advanced Ceramic for Grinding Factory Nitride Ceramic Powders Silicon Nitride
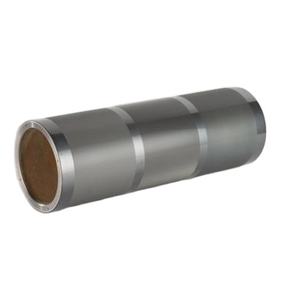
Thermocouple Protection Ceramic Tubes Si3n4 Silicon Nitride Winner 1 Set Industrial Ceramic 3.2 G/cm3 > 750 Mpa
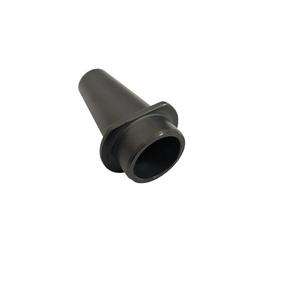
High Performance Si3N4 Spacer Wear Resistance Silicon Nitride Ceramic Parts
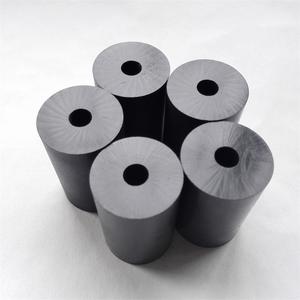