Discover Premium Ceramic Products | Durability & Elegance United | Advanced Ceramics
PRODUCT PARAMETERS
Description
Overview of Zirconium Dioxide Ceramics
Zirconium Dioxide Ceramics, known for their toughness and ability to withstand extreme temperatures, are widely used in medical, automotive, and industrial applications due to their unique properties.
Features of Zirconium Dioxide Ceramics
Exceptional fracture toughness
High thermal expansion
Excellent resistance to wear and corrosion
Biocompatibility for medical implants
(94.6% ZrO2 5.2% Y2O3 Ceramic Zirconia Beads for Grinding Media)
Specifications of 94.6% ZrO2 5.2% Y2O3 Ceramic Zirconia Beads for Grinding Media
These zirconia beads are made for grinding media. The material is 94.6% ZrO2 and 5.2% Y2O3. This mix gives high performance in industrial grinding. The beads are tough. They resist wear well. This makes them last longer than other options. They work in machines like horizontal mills or high-speed dispersers.
The beads have high density. This helps grind materials faster. They are harder than most grinding media. Hardness means less breakage. This keeps the product clean. No cracks or chips happen easily. They stay round even after long use. Shape matters for even grinding.
Chemical stability is strong. They handle acids and alkalis. No corrosion happens. This works for paints, coatings, or electronics. They stay stable in wet or dry processes. Temperature changes don’t affect them. They work in hot or cold conditions.
Sizes range from 0.1mm to 3.0mm. Small sizes grind fine particles. Bigger sizes handle coarse materials. The surface is smooth. This reduces friction. Less energy is needed. Costs go down over time.
The beads lower contamination risks. No metal impurities leak. This keeps products pure. They are good for labs or sensitive industries. Wear rates are minimal. Less material is wasted. Maintenance stays simple.
These beads suit paints, inks, cosmetics, and ceramics. They mix well in pharmaceuticals. Grinding efficiency stays high. Processing times shorten. Output quality improves.
The material composition is precise. Yttria stabilizes the zirconia. This prevents cracks during use. Crystal structure stays intact. Long-term performance stays reliable.
Choose these beads for heavy-duty grinding. They save money and time. Replacements are rare. Downtime reduces. Productivity stays consistent.
No special handling is needed. Store them in dry areas. Avoid direct heat sources. Clean them with mild solvents. Reuse them if conditions allow.
These beads meet industry standards. They pass quality tests for hardness and durability. Use them in any grinding system. They adapt to different speeds and pressures. Results stay predictable.
The design focuses on user needs. Performance matches cost. They are a practical upgrade for grinding tasks. Industries benefit from their reliability.
(94.6% ZrO2 5.2% Y2O3 Ceramic Zirconia Beads for Grinding Media)
Applications of 94.6% ZrO2 5.2% Y2O3 Ceramic Zirconia Beads for Grinding Media
94.6% ZrO2 5.2% Y2O3 ceramic zirconia beads serve as high-performance grinding media across multiple industries. The material combines zirconia dioxide with yttrium oxide for stability. This mix ensures durability under intense mechanical stress. These beads excel in grinding, dispersing, and mixing applications.
The high density of zirconia beads improves grinding efficiency. They generate strong impact forces. This breaks down particles faster. Wear resistance is a key advantage. They last longer than traditional media like steel or glass. Lower wear reduces contamination. Product purity stays high.
Chemical stability makes them suitable for harsh environments. They resist acids, alkalis, and solvents. This is critical in chemical processing. Thermal shock resistance allows use in high-temperature operations. Performance stays consistent during rapid heating or cooling.
In paints and coatings, these beads produce fine, uniform pigments. Color consistency improves. Gloss levels rise. For inks, they achieve smooth textures. Clogging in printers drops. Cosmetic manufacturers rely on them for ultrafine powders. Skin feel enhances.
Electronics benefit from precise ceramic slurry grinding. Particle size uniformity ensures reliable components. Pharmaceutical applications demand contamination-free milling. Zirconia beads meet strict hygiene standards. Active ingredients remain unaltered.
Mining operations use these beads to process minerals. High grinding efficiency lowers energy costs. Metal recovery rates increase. Environmental impact reduces due to longer bead life.
The smooth surface minimizes friction. Heat generation stays low. Energy consumption drops. Uniform bead size prevents uneven grinding. Product quality stabilizes. Maintenance intervals extend.
These beads outperform alternatives. Steel beads corrode. Glass beads break easily. Plastic beads lack density. Zirconia balances hardness and toughness. Operational costs decrease over time.
Industries prioritize efficiency and quality. 94.6% ZrO2 5.2% Y2O3 ceramic zirconia beads address both. Their adaptability suits diverse grinding needs.
Company Introduction
Advanced Ceramics founded on October 17, 2014, is a high-tech enterprise committed to the research and development, production, processing, sales and technical services of ceramic relative materials and products.. Since its establishment in 2014, the company has been committed to providing customers with the best products and services, and has become a leader in the industry through continuous technological innovation and strict quality management.
Our products includes but not limited to Silicon carbide ceramic products, Boron Carbide Ceramic Products, Boron Nitride Ceramic Products, Silicon Carbide Ceramic Products, Silicon Nitride Ceramic Products, Zirconium Dioxide Ceramic Products, Quartz Products, etc. Please feel free to contact us.(nanotrun@yahoo.com)
Payment Methods
T/T, Western Union, Paypal, Credit Card etc.
Shipment Methods
By air, by sea, by express, as customers request.
5 FAQs of 94.6% ZrO2 5.2% Y2O3 Ceramic Zirconia Beads for Grinding Media
What are zirconia beads made of?
The beads contain 94.6% zirconium dioxide (ZrO2) and 5.2% yttrium oxide (Y2O3). This mix stabilizes the zirconia structure. It ensures high strength and resistance to wear. The balance of materials supports long-term performance in grinding tasks.
Why choose these beads over others?
They last longer than alumina or steel beads. Their density is higher. This improves grinding efficiency. They resist corrosion and chemicals well. They work in wet or dry conditions. Maintenance costs drop due to reduced replacements.
Where are these beads typically used?
They suit industries needing fine grinding. Examples include paints, inks, coatings, and electronics. They process minerals, ceramics, and pharmaceuticals. They handle high-speed equipment like bead mills or stirred media mills.
How durable are they?
They are among the hardest grinding media available. Their low wear rate keeps contamination minimal. They withstand extreme temperatures and pressures. This reduces downtime for reloading or cleaning.
What size bead should I pick?
Size depends on your material’s starting fineness and target particle size. Smaller beads (0.1-0.5mm) suit nano-grinding. Larger beads (1-3mm) handle coarse materials. Match bead size to your equipment’s energy input. Test different sizes to optimize results.
(94.6% ZrO2 5.2% Y2O3 Ceramic Zirconia Beads for Grinding Media)
REQUEST A QUOTE
RELATED PRODUCTS
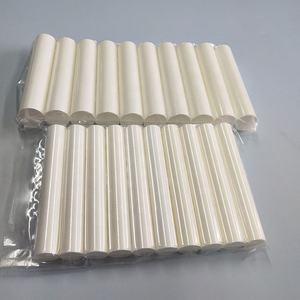
ZrO2 Factory Top Grade Thin Wall Zirconia Ceramic Tube
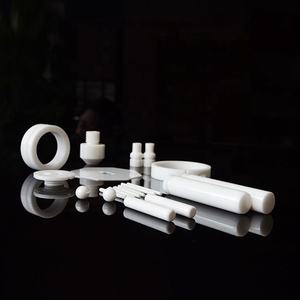
High Purity Monoclinic / Tetragonal Ultra-fine Zirconium Oxide ZrO2 Yttria Stabilized(YSZ) Zirconia Ceramic Powder
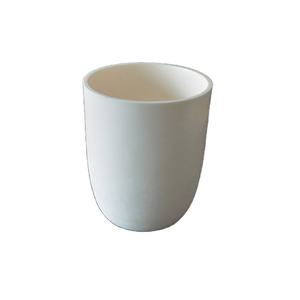
Industrial Zro2 Zirconium Oxide Zirconia Ceramic Pin/rod
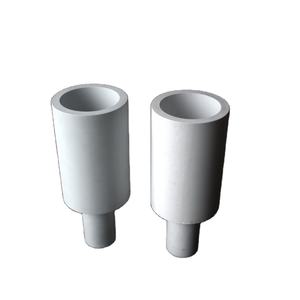
China Manufacture ZrO2 Nano Zirconium Dioxide Zirconia Nanoparticles CAS 1314-23-4 Ceramic Powder
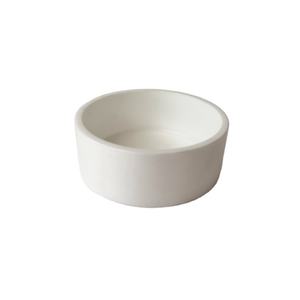
Factory Supply 99.5% ZrO2 Nano Zirconium Dioxide / Zirconium Oxide / Zirconia Nanoparticles Ceramic Powder
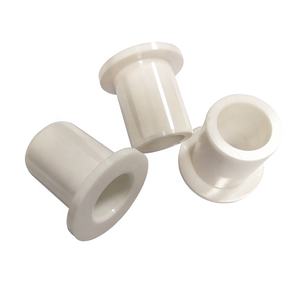