Discover Premium Ceramic Products | Durability & Elegance United | Advanced Ceramics
PRODUCT PARAMETERS
Description
Overview of Zirconium Dioxide Ceramics
Zirconium Dioxide Ceramics, known for their toughness and ability to withstand extreme temperatures, are widely used in medical, automotive, and industrial applications due to their unique properties.
Features of Zirconium Dioxide Ceramics
Exceptional fracture toughness
High thermal expansion
Excellent resistance to wear and corrosion
Biocompatibility for medical implants
(Heating Elements Zirconia Dental Furnace Sic Carbide Heater Dental Ceramic Furnace Heater)
Specifications of Heating Elements Zirconia Dental Furnace Sic Carbide Heater Dental Ceramic Furnace Heater
The Heating Elements Zirconia Dental Furnace Sic Carbide Heating unit is made for high-performance oral ceramic processing. The heater utilizes sophisticated zirconia burner. These components supply stable warmth circulation. They make certain uniform temperature level throughout the chamber. This is important for accurate sintering of dental porcelains. The zirconia product stands up to extreme temperature levels. It preserves longevity under repeated thermal cycles.
The furnace incorporates silicon carbide (Sic) heating systems. Sic heating systems warm up promptly. They attain target temperature levels much faster than standard options. Their high thermal conductivity improves power performance. The Sic product stands up to oxidation. This prolongs the heater’s life-span. It lowers upkeep costs in time. The heating unit operates successfully in settings as much as 1600 ° C. Temperature level control is managed by a digital microprocessor. The system allows exact adjustments in 1 ° C increments. Users can set several home heating accounts. These profiles fit various ceramic materials. The furnace sustains both rapid air conditioning and slow air conditioning modes. This flexibility fits different oral laboratory needs.
The chamber is developed with top quality refractory insulation. Warmth loss is lessened. Power consumption remains low. The insulation additionally enhances safety. External surfaces stay great during operation. The door includes a reinforced seal. It avoids warmth leak. It ensures consistent inner problems.
Safety systems consist of over-temperature defense. The system automatically shuts down if limits are surpassed. Voltage changes are checked. The furnace halts procedure during power instability. These features avoid damages to delicate dental materials.
Power needs vary from 220V to 240V. Standard versions sustain single-phase supply. Custom-made three-phase units are readily available for high-demand setups. The furnace connects to conventional electrical outlets. Installation calls for marginal configuration.
Maintenance involves regular cleaning of the chamber. Debris from ceramic processing is eliminated. Heating elements are evaluated monthly for wear. Substitute components are widely obtainable. Service periods depend on use frequency. Many components are made for long-lasting dependability.
(Heating Elements Zirconia Dental Furnace Sic Carbide Heater Dental Ceramic Furnace Heater)
Applications of Heating Elements Zirconia Dental Furnace Sic Carbide Heater Dental Ceramic Furnace Heater
Heating elements in zirconia oral furnaces deal with sintering zirconia products. This procedure produces solid oral restorations like crowns, bridges, and implants. The heating system heats zirconia blocks to heats. This adjustments their framework, making them sturdy enough for day-to-day use in the mouth. Exact temperature level control is important. Even tiny errors can deteriorate the final product. Zirconia heating systems depend on sophisticated heater to keep consistent heat circulation. This makes sure consistent outcomes across all repairs.
Silicon carbide (SiC) heaters prevail in dental ceramic heating systems. These heating units warmth ceramic materials made use of for veneers, inlays, and dentures. SiC heaters warm up rapidly and handle severe temperatures without breaking down. This speeds up the firing procedure. Dental labs save time while creating high-quality ceramic pieces. The product’s resistance to thermal shock matters. Frequent heating and cooling down cycles don’t harm SiC heating systems. This makes them affordable in time.
Combining zirconia and ceramic furnaces enhances oral laboratory operations. Service technicians sinter zirconia structures initially. They later on add ceramic layers for aesthetic appeals. Both heating systems call for reliable heating elements to operate appropriately. Modern heating systems enable programmable temperature curves. Individuals established specific home heating rates, hold times, and cooling prices. This customization matches the needs of various products. It minimizes errors and material waste.
Power efficiency is one more advantage. Advanced burner make use of less power while getting to target temperature levels faster. Labs reduced operating expense without compromising result top quality. The heaters’ toughness additionally reduces downtime. Regular substitutes or fixings aren’t required. This maintains production routines on track.
Safety features secure both devices and individuals. Overheat prevention systems and automatic shutoffs decrease risks. Dental specialists focus on their job without constant monitoring. Constant efficiency builds trust in the end products. Individuals receive reconstructions that fit well and last lengthy. Modern oral furnaces with enhanced heating elements meet increasing demands for precision and effectiveness. They sustain the creation of natural, useful oral options customized to patient demands.
Company Introduction
Advanced Ceramics founded on October 17, 2014, is a high-tech enterprise committed to the research and development, production, processing, sales and technical services of ceramic relative materials and products.. Since its establishment in 2014, the company has been committed to providing customers with the best products and services, and has become a leader in the industry through continuous technological innovation and strict quality management.
Our products includes but not limited to Silicon carbide ceramic products, Boron Carbide Ceramic Products, Boron Nitride Ceramic Products, Silicon Carbide Ceramic Products, Silicon Nitride Ceramic Products, Zirconium Dioxide Ceramic Products, Quartz Products, etc. Please feel free to contact us.(nanotrun@yahoo.com)
Payment Methods
T/T, Western Union, Paypal, Credit Card etc.
Shipment Methods
By air, by sea, by express, as customers request.
5 FAQs of Heating Elements Zirconia Dental Furnace Sic Carbide Heater Dental Ceramic Furnace Heater
Heating elements in zirconia dental furnaces and SiC carbide heaters for dental ceramic furnaces work under high temperatures. Here are common questions about them. What materials make up these heating elements? They use zirconia or silicon carbide. These materials handle extreme heat well. They resist damage from repeated heating cycles. Their structure stays stable even at high temperatures. Zirconia works for moderate heat ranges. Silicon carbide handles higher temperatures better.
What temperature ranges do these heaters support? Zirconia-based heaters typically reach 1200-1600°C. Silicon carbide heaters go higher, up to 1600-1800°C. The range depends on the furnace design. Dental labs choose based on the ceramic or zirconia material being processed. Higher temperatures ensure proper sintering or hardening.
How long do these heating elements last? Lifespan varies with usage. Zirconia elements last 1-3 years under normal use. Silicon carbide lasts longer, often 3-5 years. Frequent temperature changes shorten lifespan. Proper maintenance helps. Avoiding overheating or sudden cooling extends durability.
Do these heaters have safety features? Yes. Most include overheat protection. Sensors cut power if temperatures exceed limits. Insulation layers prevent external casing from getting too hot. Stable temperature control reduces risks of cracks or failures. Users should still follow operating guidelines.
How to maintain these heating elements? Clean them regularly to remove dust or debris. Check for cracks or discoloration monthly. Replace elements showing wear. Follow the furnace manual for specific care steps. Avoid touching heaters when hot. Let them cool before inspection. Proper maintenance ensures consistent performance.
(Heating Elements Zirconia Dental Furnace Sic Carbide Heater Dental Ceramic Furnace Heater)
REQUEST A QUOTE
RELATED PRODUCTS
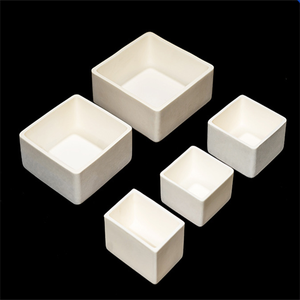
0.2mm 0.3mm 5mm 10mm 15mm 20mm G5 G10 Polished Zro2 Zirconium Oxide Zirconia Ceramic Bearing Grinding Balls and Beads
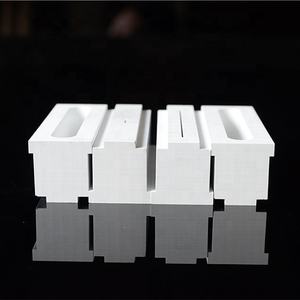
High Quality High Purity ZrO2 Zirconia Zirconium Ceramic Tubes Ceramic Zirconia
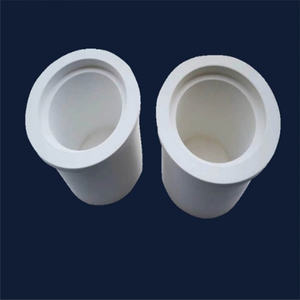
0.1mm to 50mm Grinding Ceramic Balls Zirconia Beads Used for Ball Mill
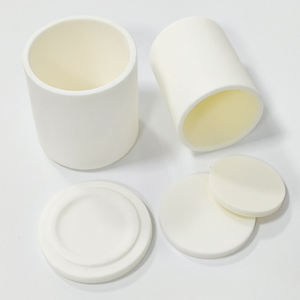
Ceramic Translucency Zro2 Blank Dental Laboratory Zirkonyum Block ultra Translucent Zirconia Ceramic Block
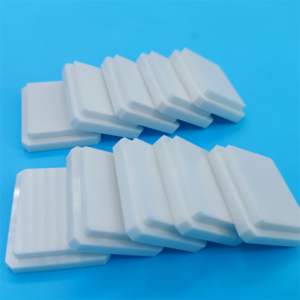
Thickness 0.635mm To 1mm 99% Al2o3 Alumina Ceramic Substrate Ceramic Plate Zirconia Plate
