Discover Premium Ceramic Products | Durability & Elegance United | Advanced Ceramics
PRODUCT PARAMETERS
Description
Overview of Zirconium Dioxide Ceramics
Zirconium Dioxide Ceramics, known for their toughness and ability to withstand extreme temperatures, are widely used in medical, automotive, and industrial applications due to their unique properties.
Features of Zirconium Dioxide Ceramics
Exceptional fracture toughness
High thermal expansion
Excellent resistance to wear and corrosion
Biocompatibility for medical implants
(Industrial Ceramic Manufacture Zirconium Oxide Part Zirconia Ceramics Sleeve)
Specifications of Industrial Ceramic Manufacture Zirconium Oxide Part Zirconia Ceramics Sleeve
Industrial ceramic manufacture zirconium oxide part zirconia porcelains sleeve offers high-performance applications requiring sturdiness and reliability. The material is zirconium oxide (ZrO2), recognized for outstanding mechanical stamina and heat resistance. The item withstands severe temperatures approximately 2400 ° F, suitable for rough industrial settings. It resists wear and corrosion, preserving performance under rough or chemically aggressive conditions.
The zirconia ceramics sleeve deals high crack strength contrasted to other ceramics. This decreases splitting threat under hefty tons or influences. Its low thermal conductivity lessens warm transfer, ideal for shielding parts in high-temperature equipment. The product’s smooth surface finish reduces friction, enhancing performance in relocating parts like pumps or bearings.
Precision production guarantees limited tolerances, with components tailored to fit specific industrial devices. Usual dimensions vary from 1mm to 500mm in size, adaptable to one-of-a-kind layout demands. The sintering process develops a dense, non-porous structure, preventing liquid or gas leak in sealing applications.
Chemical stability makes zirconia sleeves immune to acids, alkalis, and natural solvents. This fits them for chemical handling, clinical tools, and aerospace components. The product’s biocompatibility allows usage in surgical devices or oral implants without adverse responses.
Zirconia ceramics sleeves operate in oxygen-free or high-vacuum settings without breaking down. Electrical insulation properties protect against current leakage in electronic or semiconductor tools. The material’s solidity (over 1200 HV) makes sure lengthy life span even in high-stress setups like steel forming or mining.
Production makes use of advanced molding methods, consisting of injection molding and dry pressing, for regular high quality. Post-sintering therapies like grinding or polishing accomplish exact dimensions and surface area appearances. Customized layers (e.g., thermal barrier finishes) are readily available for boosted performance in specialized functions.
The product fulfills ISO 9001 requirements, making sure reliability for automobile, power, and producing fields. Testing includes hardness checks, density measurements, and thermal shock resistance tests. Lead times vary by order dimension, with bulk orders prioritized for commercial customers. Product packaging makes use of shock-resistant products to stop damage throughout delivery.
(Industrial Ceramic Manufacture Zirconium Oxide Part Zirconia Ceramics Sleeve)
Applications of Industrial Ceramic Manufacture Zirconium Oxide Part Zirconia Ceramics Sleeve
Industrial ceramic manufacture zirconium oxide part zirconia porcelains sleeves serve vital functions across multiple markets. These parts are made from zirconium dioxide, a material recognized for high strength and sturdiness. They take care of extreme temperature levels and stand up to wear successfully. This makes them ideal for rough environments where metals or plastics fail.
Zirconia porcelains sleeves prevail in equipment requiring accurate performance under stress and anxiety. They function in high-temperature heating systems, chemical processing devices, and durable engines. Their low thermal conductivity assists maintain security during quick temperature adjustments. They additionally resist deterioration from acids, alkalis, and other aggressive chemicals. This prolongs tools life-span and lowers downtime.
In vehicle and aerospace applications, zirconia sleeves safeguard moving parts from rubbing and warm. They are utilized in pump systems, shutoff components, and birthing surfaces. Their hardness prevents contortion under hefty loads. This guarantees constant procedure in engines, generators, and hydraulic systems. Their light-weight nature contrasted to metals help in gas efficiency and element layout.
The clinical area take advantage of zirconia ceramics sleeves due to their biocompatibility. They are made use of in surgical tools, dental implants, and prosthetic joints. Their smooth surface reduces bacterial development. They hold up against duplicated sanitation without degrading. This dependability is important for devices calling for long-term use in sterile atmospheres.
Electronic devices producing usages these sleeves for shielding parts in high-voltage systems. They protect against electric leak in ports and sensing units. Their security under electrical areas sustains precision in circuits and semiconductors. This reduces failure rates in critical electronic gadgets.
Zirconia ceramics sleeves adapt to personalized sizes and shapes via advanced manufacturing methods. Processes like injection molding and sintering allow tight resistances. This adaptability fulfills details demands across markets. Their cost-effectiveness in time stems from lowered substitute regularity and maintenance.
Industries prioritize zirconia porcelains sleeves for incorporating mechanical strength with chemical inertness. They resolve obstacles in extreme operating problems. Their usage boosts effectiveness, safety, and performance in complex systems.
Company Introduction
Advanced Ceramics founded on October 17, 2014, is a high-tech enterprise committed to the research and development, production, processing, sales and technical services of ceramic relative materials and products.. Since its establishment in 2014, the company has been committed to providing customers with the best products and services, and has become a leader in the industry through continuous technological innovation and strict quality management.
Our products includes but not limited to Silicon carbide ceramic products, Boron Carbide Ceramic Products, Boron Nitride Ceramic Products, Silicon Carbide Ceramic Products, Silicon Nitride Ceramic Products, Zirconium Dioxide Ceramic Products, Quartz Products, etc. Please feel free to contact us.(nanotrun@yahoo.com)
Payment Methods
T/T, Western Union, Paypal, Credit Card etc.
Shipment Methods
By air, by sea, by express, as customers request.
5 FAQs of Industrial Ceramic Manufacture Zirconium Oxide Part Zirconia Ceramics Sleeve
Zirconia ceramics sleeves are common in industrial settings. People often have questions about their use. Here are answers to five common questions.
What materials make zirconia ceramics sleeves? Zirconia ceramics sleeves use zirconium oxide powder. The powder is processed under high heat and pressure. This creates a dense, strong structure. The material has high purity, making it suitable for tough environments.
Why pick zirconia over metal or plastic sleeves? Zirconia handles extreme conditions better. It resists high temperatures, wear, and chemicals. Metal can corrode. Plastic melts under heat. Zirconia stays stable, lasts longer, and reduces replacement costs.
How hot can zirconia sleeves get before failing? Zirconia works in temperatures up to 2,200°F. It keeps strength even near melting points of metals. Thermal shock resistance prevents cracks during rapid temperature changes. This makes it ideal for furnaces or engines.
Do zirconia sleeves resist chemicals and abrasion? Yes. The material’s hardness matches steel. It avoids scratches from rough materials. Acids, alkalis, and solvents cause little damage. This suits it for chemical processing or mining equipment.
How do you install and maintain zirconia sleeves? Handle sleeves carefully. Avoid hitting them during installation. Use tools softer than zirconia to prevent surface damage. Clean with mild detergents. Check regularly for cracks or wear. Replace if surfaces degrade. Proper care ensures long service life.
(Industrial Ceramic Manufacture Zirconium Oxide Part Zirconia Ceramics Sleeve)
REQUEST A QUOTE
RELATED PRODUCTS
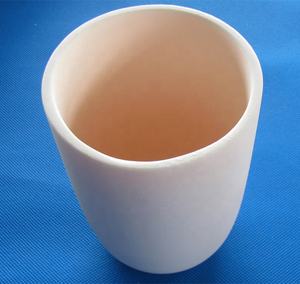
High Hardness Zirconia Ceramic Tube ZrO Ceramic Bush Sleeve
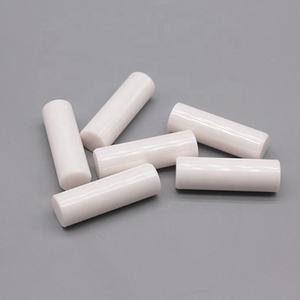
Factory Zirconia ZrO2 99.9% Cas No 1314-23-4/Bio Ceramics Nanopowder Nanoparticles/Catalyst
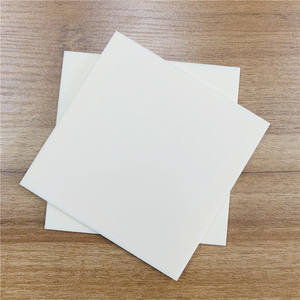
Customized Zirconia ZrO2 Ceramic Scissor Blade

Sintyron Custom Ceramic Zirconia Ceramic Ring

Al2O3 95% 99% 99.5% 99.6% 99.8% alumina zirconia ZTA ceramic piece sheet substrate high quality
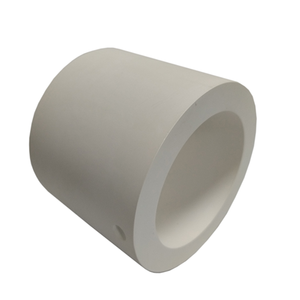