Discover Premium Ceramic Products | Durability & Elegance United | Advanced Ceramics
PRODUCT PARAMETERS
Description
Overview of Zirconium Dioxide Ceramics
Zirconium Dioxide Ceramics, known for their toughness and ability to withstand extreme temperatures, are widely used in medical, automotive, and industrial applications due to their unique properties.
Features of Zirconium Dioxide Ceramics
Exceptional fracture toughness
High thermal expansion
Excellent resistance to wear and corrosion
Biocompatibility for medical implants
(Insulation Electrical Ceramic Sheet Zirconia / Alumina Ceramic Substrate Plate Tile)
Specifications of Insulation Electrical Ceramic Sheet Zirconia / Alumina Ceramic Substrate Plate Tile
The Insulation Electrical Ceramic Sheet Zirconia / Alumina Ceramic Substrate Plate Tile serves as a high-performance solution for demanding electrical and industrial applications. These sheets combine zirconia and alumina ceramics to deliver superior insulation properties. Manufacturers use advanced processes to create dense, uniform structures with minimal porosity. This ensures reliable performance under extreme conditions. The material offers high dielectric strength, preventing electrical current leakage even at elevated voltages. Thermal stability remains excellent, withstanding temperatures up to 1600°C without losing structural integrity. Mechanical strength is a key feature, resisting cracks under heavy loads or sudden impacts. The sheets demonstrate exceptional resistance to wear, corrosion, and chemical attack, making them suitable for harsh environments. Standard thickness ranges from 0.5mm to 50mm, accommodating diverse application needs. Custom sizes up to 500mm x 500mm are available for specialized equipment. Surface finish options include polished, ground, or textured finishes to match specific requirements. Electrical insulation performance remains stable across wide temperature fluctuations. The low thermal expansion coefficient minimizes dimensional changes during rapid heating or cooling cycles. These ceramic sheets work effectively in high-voltage systems, power electronics, and industrial heating elements. They serve as ideal substrates for thin-film circuits and sensor components. Automotive industries use them for ignition systems and battery insulation. Aerospace applications benefit from their lightweight yet durable properties. Manufacturers can adjust material composition ratios to optimize thermal conductivity or electrical resistance. Alumina-rich blends provide enhanced electrical insulation, while zirconia-dominant mixes improve fracture toughness. All products undergo rigorous quality testing for density, hardness, and dielectric properties. The ceramic plates meet international standards including ASTM and IEC certifications. Customized machining services allow for precise drilling, cutting, or shaping to fit complex assemblies. Bulk orders receive tailored packaging to prevent damage during shipping. Technical support teams assist with material selection and application-specific design challenges.
(Insulation Electrical Ceramic Sheet Zirconia / Alumina Ceramic Substrate Plate Tile)
Applications of Insulation Electrical Ceramic Sheet Zirconia / Alumina Ceramic Substrate Plate Tile
Insulation electrical ceramic sheets made from zirconia and alumina are widely used in industries needing strong heat resistance and electrical insulation. These materials handle high temperatures well. They keep working reliably in environments where other insulators might fail. Zirconia ceramic sheets stand out because they resist extreme heat and wear. They are often chosen for jobs requiring long-lasting performance under stress. Alumina ceramic sheets offer excellent electrical insulation. They are cost-effective for everyday industrial uses. Both types prevent energy loss. They make electronic systems safer and more efficient.
In electronics, these ceramic sheets act as substrates for circuits. They manage heat from components like power transistors and LEDs. This prevents overheating and extends device life. The sheets are non-conductive. They stop electrical currents from leaking. This protects sensitive parts from damage.
High-temperature furnaces and aerospace systems rely on these ceramics. They insulate components exposed to intense heat. Jet engines and rocket parts use them to handle thermal shocks. The ceramics stay stable even when temperatures change rapidly. Automotive systems use them in sensors and ignition components. They endure engine heat and electrical loads. This improves vehicle reliability.
Medical equipment benefits from zirconia and alumina sheets. They are chemically inert. They do not react with harsh disinfectants or bodily fluids. This makes them safe for tools like imaging devices and surgical instruments. Their smooth surface resists bacteria buildup. This helps maintain sterile conditions.
Industrial machinery uses these ceramics as liners or coatings. They protect metal parts from corrosion and abrasion. Manufacturing processes involving molten metals or chemicals use them to shield equipment. Their durability reduces downtime and maintenance costs.
These ceramic sheets are customizable in thickness and shape. Manufacturers tailor them to fit specific applications. They are compatible with advanced manufacturing techniques like laser cutting. This allows precise integration into complex designs. Their versatility makes them essential in modern engineering.
Company Introduction
Advanced Ceramics founded on October 17, 2014, is a high-tech enterprise committed to the research and development, production, processing, sales and technical services of ceramic relative materials and products.. Since its establishment in 2014, the company has been committed to providing customers with the best products and services, and has become a leader in the industry through continuous technological innovation and strict quality management.
Our products includes but not limited to Silicon carbide ceramic products, Boron Carbide Ceramic Products, Boron Nitride Ceramic Products, Silicon Carbide Ceramic Products, Silicon Nitride Ceramic Products, Zirconium Dioxide Ceramic Products, Quartz Products, etc. Please feel free to contact us.(nanotrun@yahoo.com)
Payment Methods
T/T, Western Union, Paypal, Credit Card etc.
Shipment Methods
By air, by sea, by express, as customers request.
5 FAQs of Insulation Electrical Ceramic Sheet Zirconia / Alumina Ceramic Substrate Plate Tile
What materials make up insulation electrical ceramic sheets?
These sheets use zirconia or alumina. Both materials handle high heat. They resist electricity well. This makes them safe for circuits. They last longer than plastic or metal options.
How much heat can these ceramic sheets handle?
Zirconia sheets work up to 2000°C. Alumina handles around 1700°C. Exact limits depend on thickness. They stay stable under heat. This stops warping or cracking.
Where are these ceramic sheets commonly used?
They fit electronics needing insulation. Examples include circuit boards, heaters, sensors. Factories use them in furnaces. Labs apply them in high-temperature tests. They protect parts from electrical leaks.
Why pick zirconia over alumina or the reverse?
Zirconia is tougher. It resists cracks better under stress. Alumina costs less. It works for basic insulation needs. Choose zirconia for extreme conditions. Alumina suits everyday high-heat tasks.
How do I install these sheets correctly?
Clean the surface first. Remove dust or grease. Use adhesives rated for high heat. Clamp the sheet tightly while drying. Avoid drilling near edges. Test for secure bonding before full use.
(Insulation Electrical Ceramic Sheet Zirconia / Alumina Ceramic Substrate Plate Tile)
REQUEST A QUOTE
RELATED PRODUCTS
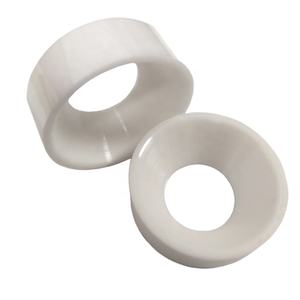
Zirconium Dioxide For Ceramics And Glass Zirconia White Fume Silica 92%
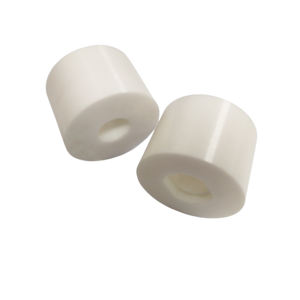
Ceramic Raw Material Zrsio4 Zirconia Silicate Powder 65% White Zirconium Silicate Powder for Ceramic
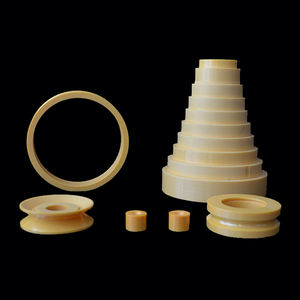
Nano Zirconium Oxide Zirconia Powder Nano Zirconium Dioxide CAS 1314-23-4 Ceramic Powder
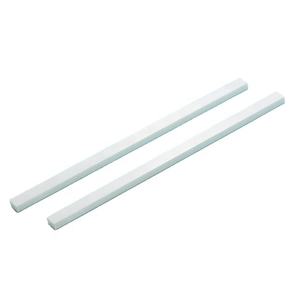
1.5mm Thin Black ZrO2 Cylinder Ceramic Ferrule Zirconia Ring
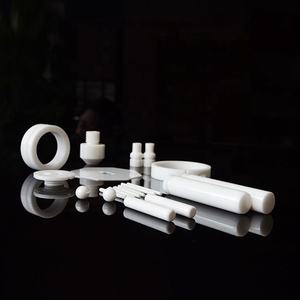
High Purity Monoclinic / Tetragonal Ultra-fine Zirconium Oxide ZrO2 Yttria Stabilized(YSZ) Zirconia Ceramic Powder
