Discover Premium Ceramic Products | Durability & Elegance United | Advanced Ceramics
PRODUCT PARAMETERS
Description
Overview of Zirconium Dioxide Ceramics
Zirconium Dioxide Ceramics, known for their toughness and ability to withstand extreme temperatures, are widely used in medical, automotive, and industrial applications due to their unique properties.
Features of Zirconium Dioxide Ceramics
Exceptional fracture toughness
High thermal expansion
Excellent resistance to wear and corrosion
Biocompatibility for medical implants
(Zirconium Oxide Ceramic Beads for Paint Zirconium Silicate Wet Ball Milling Zirconia Ball 10 mm)
Specifications of Zirconium Oxide Ceramic Beads for Paint Zirconium Silicate Wet Ball Milling Zirconia Ball 10 mm
Zirconium oxide ceramic beads are created for applications like paint diffusion, zirconium silicate handling, and wet round milling. These 10 mm zirconia rounds offer high efficiency in grinding and mixing tasks. The material structure is zirconium oxide (ZrO2) with added stabilizers like yttria. This makes sure remarkable durability and resistance to use. The grains have a thickness of around 6.0 g/cm ³, making them much heavier than many options. Their high density enhances grinding efficiency by using better pressure during milling.
The hardness of these grains gets to 9 on the Mohs scale. This decreases particle contamination in refined products. The reduced wear rate prolongs the lifespan of both the grains and milling equipment. The round shape and accurate 10 mm size guarantee uniform contact with resources. This consistency creates better particle distributions in much shorter durations.
Zirconium oxide ceramic beads withstand chemical deterioration. They work well in acidic or alkaline settings common in paint and layer production. Thermal stability allows operation at temperatures approximately 1,500 ° C without architectural deterioration. This makes them suitable for high-heat commercial processes.
The smooth surface of the beads decreases rubbing during milling. Energy consumption decreases while refining speed increases. These grains surpass traditional grinding media like steel or glass. They create less warm, stopping material deterioration in delicate applications.
Applications include paints, inks, porcelains, and digital components. The 10 mm dimension balances effect force and surface area for medium-viscosity mixtures. Users attain optimal lead to both upright and straight mills. Very little maintenance is needed because of the grains’ resistance to breaking and splitting.
Production utilizes sophisticated sintering methods to ensure consistent microstructure. This eliminates inner flaws that could jeopardize efficiency. Quality assurance checks assure roundness and dimension precision. Each set satisfies strict sector requirements for uniformity.
Replacement intervals are longer compared to options. This decreases downtime and operational prices. The inert nature of zirconium oxide avoids reactions with refined products. End products preserve pureness and preferred chemical homes.
These grains are cost-effective over long-term usage. First investment is countered by decreased wear and greater processing performance. Industries calling for specific bit dimension control advantage most from this option. Compatibility with various milling systems makes sure wide usability.
(Zirconium Oxide Ceramic Beads for Paint Zirconium Silicate Wet Ball Milling Zirconia Ball 10 mm)
Applications of Zirconium Oxide Ceramic Beads for Paint Zirconium Silicate Wet Ball Milling Zirconia Ball 10 mm
Zirconium oxide ceramic grains are widely made use of in industrial grinding procedures. These beads function as grinding media in paint manufacturing, zirconium silicate handling, and damp sphere milling applications. The 10 mm zirconia spheres are a preferred option for their equilibrium of size and performance. They give reliable material malfunction while preserving item high quality.
The high thickness of zirconium oxide makes these beads reliable for grinding tough products. Their wear resistance ensures marginal loss during milling. This minimizes the demand for frequent replacements. The beads maintain regular sizes and shape over long periods. This uniformity leads to consistent bit distribution in the final product.
In paint manufacturing, zirconia ceramic beads aid accomplish smooth, fine surfaces. They avoid contamination as a result of their chemical inertness. This is crucial for keeping shade accuracy and security. The grains work well with both water-based and solvent-based paints. They manage high-speed milling without fracturing.
For zirconium silicate processing, the 10 mm grains supply optimum impact power. This accelerates the grinding process. It likewise decreases power consumption compared to standard grinding media. The beads’ solidity ensures very little wear even with abrasive products. This prolongs equipment life and minimizes maintenance expenses.
Wet round milling take advantage of the beads’ resistance to deterioration and chemical attack. They carry out dependably in liquid settings. The spherical shape of the 10 mm beads advertises efficient movement within the mill. This improves grinding effectiveness and reduces handling time.
Zirconium oxide ceramic beads outperform options like steel or glass grains. They create much less heat during milling. This avoids thermal damages to delicate materials. Their non-porous surface area avoids material build-up. This streamlines cleaning and reduces cross-contamination dangers.
The 10 mm size is excellent for numerous commercial mills. It stabilizes surface area and impact force. Smaller sized beads might lack grinding power. Larger grains could reduce milling efficiency. The 10 mm grains strike a useful middle ground.
Price cost savings come from the grains’ lengthy life span. Fewer substitutes mean lower functional prices. Their toughness also reduces downtime. This sustains continuous production cycles.
Environmental advantages include reduced waste generation. The grains’ longevity suggests less product winds up in land fills. Their manufacturing process has a reduced carbon impact compared to metal alternatives.
Industries relying on precision grinding support zirconium oxide ceramic grains. These consist of paints, layers, porcelains, and electronic devices. The 10 mm zirconia rounds fulfill the needs of high-performance milling. They provide reliability, effectiveness, and quality throughout varied applications.
Company Introduction
Advanced Ceramics founded on October 17, 2014, is a high-tech enterprise committed to the research and development, production, processing, sales and technical services of ceramic relative materials and products.. Since its establishment in 2014, the company has been committed to providing customers with the best products and services, and has become a leader in the industry through continuous technological innovation and strict quality management.
Our products includes but not limited to Silicon carbide ceramic products, Boron Carbide Ceramic Products, Boron Nitride Ceramic Products, Silicon Carbide Ceramic Products, Silicon Nitride Ceramic Products, Zirconium Dioxide Ceramic Products, Quartz Products, etc. Please feel free to contact us.(nanotrun@yahoo.com)
Payment Methods
T/T, Western Union, Paypal, Credit Card etc.
Shipment Methods
By air, by sea, by express, as customers request.
5 FAQs of Zirconium Oxide Ceramic Beads for Paint Zirconium Silicate Wet Ball Milling Zirconia Ball 10 mm
Zirconium oxide ceramic beads are grinding media used in ball milling processes. They are made from zirconium oxide. They are 10 mm in size. They are ideal for applications like paint production. They help achieve fine particle sizes. Here are common questions about these beads.
What are zirconium oxide ceramic beads? These beads are high-performance grinding media. They are made from zirconium oxide powder. They are sintered at high temperatures. They have high density and wear resistance. They are used in wet ball milling. They work well in industries like coatings and ceramics.
Why choose zirconium oxide beads over other grinding media? These beads last longer than alternatives. They resist wear better. They stay round during use. This keeps milling efficient. They do not crack easily. They reduce contamination risks. They save costs over time.
Why use zirconium oxide beads for paint milling? Paint requires even particle sizes. These beads grind pigments smoothly. They prevent overheating. This protects paint quality. They do not react with chemicals. They keep colors pure. They work fast. This speeds up production.
How to maintain zirconium oxide beads? Clean beads after each use. Check for broken pieces. Remove damaged beads. Store them dry. Avoid sudden temperature changes. Replace worn beads regularly. Proper care extends their life.
What is the difference between zirconium oxide and zirconium silicate beads? Zirconium oxide beads are harder. They last longer. Zirconium silicate beads are cheaper. They suit less demanding tasks. Oxide beads handle high-intensity milling. Silicate beads wear faster. Choose based on budget and needs.
These beads improve milling efficiency. They ensure consistent results. They are reliable for industrial applications. Users report better product quality. They reduce downtime. They lower long-term costs.
(Zirconium Oxide Ceramic Beads for Paint Zirconium Silicate Wet Ball Milling Zirconia Ball 10 mm)
REQUEST A QUOTE
RELATED PRODUCTS
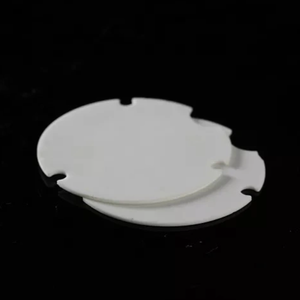
Zirconia Ceramic Guide Wheel, Precision Ceramic Parts,good Quality Zirconia Ceramic
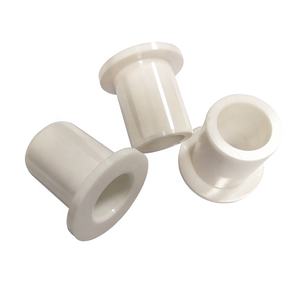
2025 Full Ceramic Bearings 8x22x7mm for Inline Skate Washable Deep groove Ball 608 Ceramic Ball White Zirconia ZrO2 Ball Bearing
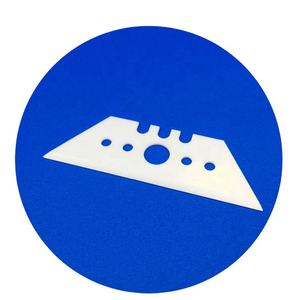
Manufacturing High Temp Resistant Y2O3 Y-TZP Zirconia Ceramic Polishing Rods Bar
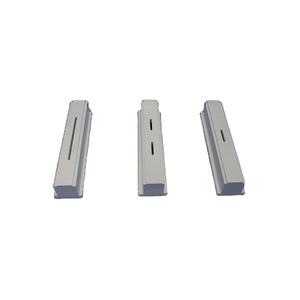
Custom ZrO2 Disc Polished Zirconia Ceramic Plate Zirconia Sheet Board
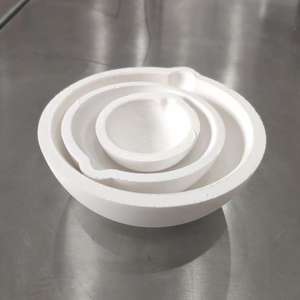
Customized ZrO2 Zirconia Ceramic Plate Structure Component Strip
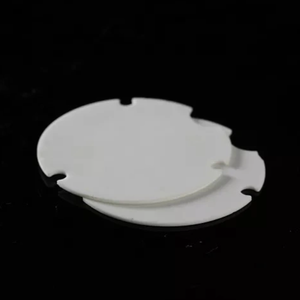